Turning Cow Manure Into Plastic
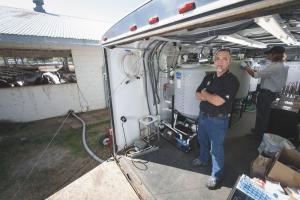 ✖  |
A 21-letter word that’s almost impossible to pronounce is the source of a new kind of plastic used to make nursery pots, landscape matting and packaging materials. Polyhydroxyalkanoate (known as PHA) is being produced from liquid cow manure at the University of Idaho’s Civil Engineering department. Dr. Erik Coats is the Associate Professor in charge of the pilot program and a team of students that’s turning about 10 gal. of manure a day into a few pounds of plastic.
“Our process works by fermenting liquid manure to convert carbohydrates into organic acids,” says Coats. “Liquid is separated from the solids, and bacteria used in wastewater treatment plants is added to the liquids and then oxygenated. Bacteria consume the organic acids and produce a small granule, which is raw plastic, similar to polyethylene and polypropylene.” Coats says that PHA, unlike the petroleum-based plastics, is biodegradable.
Coats and his team built a portable pilot-scale system that was tested at the University of Idaho dairy in the fall of 2013 with favorable results. They plan to have a scale model system operational by the spring of 2014 to be tested at a dairy in southeast Idaho.
“It’s been an exciting project for our department and the students involved,” says Coats. “We think dairy manure is a great untapped resource in Idaho and other dairying states.” Coats and his team are also studying the material characteristics and properties of PHA in more detail to better understand potential commercial applications. Idaho has about 550,000 milking cows, each one producing more than 100 lbs. of manure a day.
“With PHA selling at a premium price, there’s definitely an opportunity for significant economic return for dairies if our system proves successful,” says Coats. “We’re hoping that the technology can be deployed at full-scale dairies in 3 to 5 years.”
Funding for the test project was provided by the Idaho Dairymen’s Association, the Idaho National Lab, the National Science Foundation and Idaho’s Higher Education Research Council. His research team includes masters and doctoral students in civil engineering and biochemistry.
Contact: FARM SHOW Followup, Erik Coats, Civil Engineering Department, University of Idaho, 875 Perimeter Dr., MS 1022, Moscow, Idaho 83844 (ph 208 885-6782; civilengr@uidaho.edu).
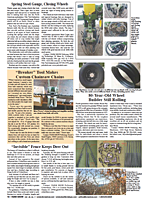
Click here to view page story appeared in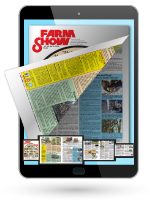
Click here to read entire issue
Turning Cow Manure Into Plastic MANURE HANDLING Miscellaneous A 21-letter word that’s almost impossible to pronounce is the source of a new kind of plastic used to make nursery pots landscape matting and packaging materials Polyhydroxyalkanoate known as PHA is being produced from liquid cow manure at the University of Idaho’s Civil Engineering department Dr Erik Coats is the Associate Professor in charge of the pilot program and a team of students that’s turning about 10 gal of manure a day into a few pounds of plastic “Our process works by fermenting liquid manure to convert carbohydrates into organic acids ” says Coats “Liquid is separated from the solids and bacteria used in wastewater treatment plants is added to the liquids and then oxygenated Bacteria consume the organic acids and produce a small granule which is raw plastic similar to polyethylene and polypropylene ” Coats says that PHA unlike the petroleum-based plastics is biodegradable Coats and his team built a portable pilot-scale system that was tested at the University of Idaho dairy in the fall of 2013 with favorable results They plan to have a scale model system operational by the spring of 2014 to be tested at a dairy in southeast Idaho “It’s been an exciting project for our department and the students involved ” says Coats “We think dairy manure is a great untapped resource in Idaho and other dairying states ” Coats and his team are also studying the material characteristics and properties of PHA in more detail to better understand potential commercial applications Idaho has about 550 000 milking cows each one producing more than 100 lbs of manure a day “With PHA selling at a premium price there’s definitely an opportunity for significant economic return for dairies if our system proves successful ” says Coats “We’re hoping that the technology can be deployed at full-scale dairies in 3 to 5 years ” Funding for the test project was provided by the Idaho Dairymen’s Association the Idaho National Lab the National Science Foundation and Idaho’s Higher Education Research Council His research team includes masters and doctoral students in civil engineering and biochemistry Contact: FARM SHOW Followup Erik Coats Civil Engineering Department University of Idaho 875 Perimeter Dr MS 1022 Moscow Idaho 83844 ph 208 885-6782; civilengr@uidaho edu
To read the rest of this story, download this issue below or click
here to register with your account number.