2014 - Volume #38, Issue #3, Page #36
[ Sample Stories From This Issue | List of All Stories In This Issue | Print this story
| Read this issue]
Unusual Fix For Grain Auger Equipped With Honda Gas Engine
Roger Gutschmidt, Gackle, N. Dak.: “A customer brought me a 7-in. dia. by 35-ft. Brandt grain auger equipped with a Honda gas engine. He said the auger vibrated a lot and that after running empty for 10 min. or so it would lock up and kill the engine. “I figured the problem had to be with either the auger flighting, the bearings on the top shaft, the drive chain, or the gearbox.
“The first thing I did was take the gearbox apart. I thought for sure I’d find a broken gear or a bad bearing, but when I drained the oil and examined everything it all looked fine. Then I removed the auger flighting, pulling all 35 ft. out of the tube. I examined the entire length of the auger on my hands and knees, expecting to find broken welds and loose auger flighting, but everything looked good. Then I rolled the tube on a nice, flat surface to check for any bends, but it was perfectly straight.
“I also used a flashlight to look inside the auger tube from both ends to see if there were any obstructions or dents I had missed, but found none.
“So I put it back together, started the engine, and engaged the drive belt. The auger vibrated so much I thought it was going to fly apart. Now I was really stumped. I started asking around at other repair shops, friends, and anyone else I could think of as to why this auger was vibrating so badly.
“I finally pulled the auger flighting out one more time and really looked it over carefully, thinking that maybe I had overlooked something obvious the first time. I still found nothing, so I put it all back together again. I even put new bearings, races and seals in the gearbox.
“I was at the end of my rope. I had put more than 15 hrs. of my time into this project but still hadn’t figured it out. I finally had to tell the customer to come and get it. I’ve been doing welding and repair work for more than 40 years but had never run across anything like this.
“Well, the customer took the auger to a nearby competitor’s repair shop. He removed the auger flighting and made new welds between all the existing welds along the entire length of the auger. I asked myself, ‘Why would you do that?’ when it was clearly evident that sufficient welds were already there. And I thought if those welds were necessary, why didn’t the factory weld it that way?
“He told the customer that based on his experience, this welding procedure takes care of such vibration problems. Vibration like this is especially bad on big swing augers. He does this welding trick, and it takes care of the problem every time.
“Well, that was a new one to me. I would never have thought of doing that. So now those welds are spaced every 6 in. on both sides the entire length of the auger, instead of 12 in. I’m still in denial, and can’t believe this welding job did the trick. But the auger doesn’t vibrate any more and the problem is solved. I’m dumbfounded and hope I don’t run into my competitor any time soon because he’ll certainly rub it in. These are the kind of repair problems that keep one humble.”
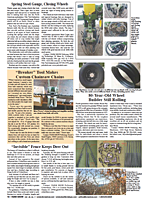
Click here to download page story appeared in.
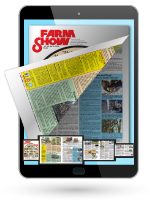
Click here to read entire issue
To read the rest of this story, download this issue below or click here to register with your account number.