"Slow Conveyor" System Helps Select Seed Corn By Hand
Rich Holman’s low-cost seed handling system fits his approach to seed. The organic dairyman and seedsman has spent the past 12 years developing 2 lines of open-pollinated corn for his use and for a growing number of customers. Since keeping costs down is key to the operation, he designed and assembled a low-cost processing system.
“I have it set up so the system unloads automatically, allowing me to go through and hand select ears to save for seed,” explains Holman.
He started with a used IH-mounted picker. Holman used the elevator and the husking beds, mounting the elevator to the side of a covered chopper box. The husking beds, a sorting table, and an unloading conveyor belt are suspended off the floor inside the box.
“I pick with a Uni Harvester and an old Farmhand chopper box with an unloading auger,” explains Holman. “They are known for smooth unloading.”
When the wagon is full, Holman pulls alongside the picker elevator. To ensure slow unloading, he mounted a gearbox with a 5 hp. electric motor to run the unloading auger.
“It feeds the ears very slowly into the picker’s elevator,” he says. “The elevator, husking beds and conveyer are all electric and controlled from a breaker box also mounted in the chopper box.”
Ears coming out of the elevator feed through from one husking bed to the other. As they come out of the second husking bed, they land on a sorting table with the husks being discharged to the floor.
“I toss soft ears or ears with the husk still on to the floor,” says Holman. “It is a simple process, but one that has helped me reduce maturity on my line of Minnesota 13 corn from more than 100 days to 88 days.”
The good ears are tossed onto a rubber conveyer belt with paddles that carry them to a gravity box. Once the gravity box is full, the ears selected by eye and feel are transferred to a floored bin. Supplemental heat completes the drying process.
“After a couple of hours, the corn and husks are often too deep for me to stand in,” says Holman. “Since the chopper box still has its apron in it, I climb out and run the husks and rejected ears into a grinder to make feed for my dairy herd.”
The chopper box roof eliminates the need for permanent storage of the processing system. A light over the sorting table allows Holman to process his seed corn ears even at night.
“I’ve been selling certified, organic seed corn for more than 6 years,” says Holman. “This processing system makes it possible for me to select only the best ears for seed. When it is running, my hands are flying and so are the ears.”
Contact: FARM SHOW Followup, Breezy Hills Farm, 1945 60th Ave., Baldwin, Wis. 54002 (ph 715 684-2488 or 715 410-1060; imph59@gmail.com).
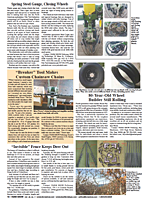
Click here to download page story appeared in.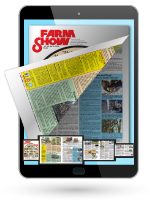
Click here to read entire issue
Slow Conveyor System Helps Select Seed Corn By Hand CROPS Miscellaneous Rich Holman’s low-cost seed handling system fits his approach to seed The organic dairyman and seedsman has spent the past 12 years developing 2 lines of open-pollinated corn for his use and for a growing number of customers Since keeping costs down is key to the operation he designed and assembled a low-cost processing system “I have it set up so the system unloads automatically allowing me to go through and hand select ears to save for seed ” explains Holman He started with a used IH-mounted picker Holman used the elevator and the husking beds mounting the elevator to the side of a covered chopper box The husking beds a sorting table and an unloading conveyor belt are suspended off the floor inside the box “I pick with a Uni Harvester and an old Farmhand chopper box with an unloading auger ” explains Holman “They are known for smooth unloading ” When the wagon is full Holman pulls alongside the picker elevator To ensure slow unloading he mounted a gearbox with a 5 hp electric motor to run the unloading auger “It feeds the ears very slowly into the picker’s elevator ” he says “The elevator husking beds and conveyer are all electric and controlled from a breaker box also mounted in the chopper box ” Ears coming out of the elevator feed through from one husking bed to the other As they come out of the second husking bed they land on a sorting table with the husks being discharged to the floor “I toss soft ears or ears with the husk still on to the floor ” says Holman “It is a simple process but one that has helped me reduce maturity on my line of Minnesota 13 corn from more than 100 days to 88 days ” The good ears are tossed onto a rubber conveyer belt with paddles that carry them to a gravity box Once the gravity box is full the ears selected by eye and feel are transferred to a floored bin Supplemental heat completes the drying process “After a couple of hours the corn and husks are often too deep for me to stand in ” says Holman “Since the chopper box still has its apron in it I climb out and run the husks and rejected ears into a grinder to make feed for my dairy herd ” The chopper box roof eliminates the need for permanent storage of the processing system A light over the sorting table allows Holman to process his seed corn ears even at night “I’ve been selling certified organic seed corn for more than 6 years ” says Holman “This processing system makes it possible for me to select only the best ears for seed When it is running my hands are flying and so are the ears ” Contact: FARM SHOW Followup Breezy Hills Farm 1945 60th Ave Baldwin Wis 54002 ph 715 684-2488 or 715 410-1060; imph59@gmail com
To read the rest of this story, download this issue below or click
here to register with your account number.