You have reached your limit of 3 free stories. A story preview is shown instead.
To view more stories
(If your subscription is current,
click here to Login or Register.)
5-Ft. Round Baler Cut Down To 4-Ft.
Charles Axelson, Finlayson, Minn., bought a used Vermeer 605 C round baler and used it for a year to make standard 5-ft. wide bales. Then his hay buyers started asking him for 4-ft. bales.
“Many local horse owners have 8-ft. trailers, so they can haul two rows of 4-ft. wide bales without worrying about having
..........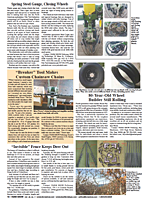
You must sign in, subscribe or renew to see the page.
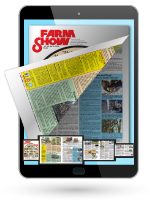
You must sign in, subscribe or renew to see the flip-book
5-Ft Round Baler Cut Down To 4-Ft BALERS Charles Axelson Finlayson Minn bought a used Vermeer 605 C round baler and used it for a year to make standard 5-ft wide bales Then his hay buyers started asking him for 4-ft bales “Many local horse owners have 8-ft trailers so they can haul two rows of 4-ft wide bales without worrying about having an oversize load I didn’t want to spend the money for a new baler so I converted the 5-ft model I already had to make 4-ft bales ” says Axelson He removed all the bale-forming belts belt guides and rollers from the bale chamber The bottom rollers are designed to work “in time” so he used a center punch to mark the top center before he pulled them out He also unbolted the pickup With the rollers pulled he used threaded rod and flat iron to hold the baler’s walls in place He jacked the baler up and put a roller under each side of the axle Then he used a cutting torch to cut 1 ft out of the center of the axle Then a come-along was used to draw the right side of the baler over to the left Once the walls were square he pulled the 2 parts of the axle together and braced them with angle iron and threaded rod He cut off part of the tongue on each side of the baler’s main frame to narrow it up then pulled the frame in and welded a 1/4-in thick plate onto it He also slid the baler’s main brace back and welded a 1/4-in thick steel plate onto it He cut 12 in off all the roller shafts and roller tubes and welded them back together He cut the belt guide down to 48 in put a rod inside and welded it on The final step was to reassemble all the belts rollers and guides “I think you could make this conversion on any baler And you don’t need fancy equipment to do the job ” says Axelson “I used a bandsaw in my garage to cut all the tubes and shafts I also used an old 180-amp welder and a set of cutting torches Pioneer Machine Shop in Aitkin Minn helped me with some of the rollers ” Blueprints and photos of the process are available for a fee Contact: FARM SHOW Followup Charles Axelson 17665 160th Lane Finlayson Minn 55735 ph 320 592-3107; a_axelson@msn com
To read the rest of this story, download this issue below or click
here to register with your account number.