You have reached your limit of 3 free stories. A story preview is shown instead.
To view more stories
To view more stories
SUBSCRIBE OR RENEW NOW
(If your subscription is current, click here to Login or Register.)2014 - Volume #38, Issue #6, Page #7
[ Sample Stories From This Issue | List of All Stories In This Issue]
On-Farm Fiber Mill Takes Any Size Order
Margie and Jim Schafer recently opened their on-farm fiber processing plant with a promise to process every order separately, no matter how small. If you send in a fleece from 3 separate sheep as 3 separate orders, you’ll get 3 separate orders of washed and carded fiber back. Other processes like spinning require more ..........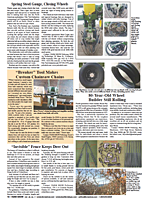
You must sign in, subscribe or renew to see the page.
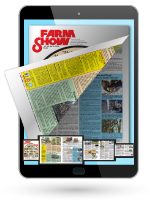
You must sign in, subscribe or renew to see the flip-book
On-Farm Fiber Mill Takes Any Size Order FARM HOME Clothes Margie and Jim Schafer recently opened their on-farm fiber processing plant with a promise to process every order separately no matter how small If you send in a fleece from 3 separate sheep as 3 separate orders you’ll get 3 separate orders of washed and carded fiber back Other processes like spinning require more than a single fleece “Our smallest order so far has been the fiber from a single rabbit ” laughs Margie “Our primary customer base is small farmers and shepherds with a few animals Our secondary market is fiber artists like hand spinners weavers knitters and crocheters They may want a fleece from an individual animal processed separately Unlike some big fiber mills we’re set up to do that ” Although the Schafers just opened the Round Barn Fiber Mill this fall they’re already booked ahead 2 to 3 mo with orders They report that being booked ahead 9 mo is not unusual in the business They have heard of one mill that is booked ahead for 2 years “We have already added staff and will add equipment if necessary ” says Jim “We want to keep the wait down We are ramping up as fast as we can but the amount of work we got just starting was amazing We got into the market well after shearing and still have a thousand pounds of fleece to process ” In fact it was the long waits for processing that started them thinking about setting up a mill “We bought our farm and started raising American Jacob sheep ” says Margie “I visited a shepherd who also had a mill and it fit with my interest in sheep and fiber arts and our interest in having a home-based business There seemed to be room for more mills so we started looking into it ” The Shafers say they are in the business for the long run having invested a quarter million dollars in new equipment Jim acknowledges that margins are low but their business plan is positive in part because they recently sold another business They had the capital to invest in new equipment which gave them access to technical support “A lot of people buy used equipment ” says Jim “However the learning curve is so steep that without the extra help and support I don’t know if we could have done it Now that we’ve been through a startup we might not be afraid of used equipment “ Services offered include washing fleeces in a special machine or by hand if needed in 175°F water to clean the wool and remove lanolin Once the fleeces are dried they go through a picker that opens the locks and prepares them for carding The carding machine takes picked fibers and aligns them into parallel format and removes most remaining dirt or foreign material The carding machine can produce roving long strips of carded fiber that hand spinners use cloud fiber more open and also can be spun or batts can be spun or used for quilts or felting For those customers who want their fiber processed even further it can be pindrafted Here sharp metal combs convert roving into more parallel and longer fibers called semi-worsted fibers Non-spinners can have their fiber spun into single strands that can then be plied together into 2 or 3-ply yarn The yarn can be run through a cone winder or a skein winder depending on the end user s preference The final machine in the Round Barn s lineup is a core- spun rug yarn maker It is an attachment to the carding machine that makes coarse rug yarn fiber that has been spun around a cotton core to make a bulky novelty yarn The textile industry in this country disappeared as jobs went overseas but I like to think it is coming back through small mills like ours says Jim We can t compete with China as a commercial mill but we can do okay providing a service for small farmers Margie advises interested customers to visit the Round Barn website or call with questions There is a lot of information on preparing the fleece on the website as well as order blanks that can be downloaded Eventually the Shafers hope to sell finished product as well as services One of our goals is to develop lines of wool from heritage or endangered breeds says Margie If we can help the owners improve their returns it may help the breeds as well Contact: FARM SHOW Followup Round Barn Fiber Mill 10123 Freeport Road Durand Ill 61024 ph 815 201-1800; help@roundbarnfiber com; www roundbarnfiber com
To read the rest of this story, download this issue below or click here to register with your account number.