You have reached your limit of 3 free stories. A story preview is shown instead.
To view more stories
(If your subscription is current,
click here to Login or Register.)
Swiveling Crane Makes Log Handling Easy
“I use an outdoor wood burning furnace to heat my home, so I split a lot of wood. My home-built swivel crane makes the job a lot easier,” says Norman Bennett, Newport Vt.
Bennett has logs delivered to his home where they’re dumped into a big pile. Separating them out with a Peavey hook was a dangerous, difficul
..........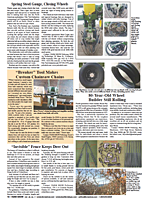
You must sign in, subscribe or renew to see the page.
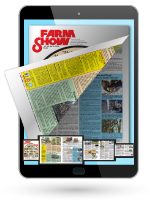
You must sign in, subscribe or renew to see the flip-book
Swiveling Crane Makes Log Handling Easy WOODLOT EQUIPMENT Miscellaneous “I use an outdoor wood burning furnace to heat my home so I split a lot of wood My home-built swivel crane makes the job a lot easier ” says Norman Bennett Newport Vt Bennett has logs delivered to his home where they’re dumped into a big pile Separating them out with a Peavey hook was a dangerous difficult job So he built a 30-ft tall swiveling crane with an electric winch A 28-ft long gib pins onto the base of a 30-ft high pole The gib is free to swivel on an underground base made from a modified pickup axle and has a 5 000-lb electric winch mounted about halfway up it Bennett uses a remote control to lift the log off the pile then manually rotates the gib and lowers the log onto a conveyor located next to his shed From there he saws the logs into 2-ft blocks splits them and stacks them by hand in the shed “It really works slick The gib is strong enough to lift logs up to 30 in dia and 16 ft long ” says Bennett “It’s patterned after the kind of cranes granite quarries in our area use to raise huge rocks weighing up to 100 tons The pole is supported by 3 guide wires at the top It swivels where the guide wires attach to it “I use a foot-operated switch to advance the conveyor I stand at the end of the conveyor and move the log about 3 ft at a time as I cut the log into 2-ft blocks which then slide down on rollers toward the splitter I fill the shed from one end to the other and as I go along I reposition the conveyor If I want I can even use the crane to move the conveyor I use a hand-operated winch to raise and lower the gib ” He used I-beams off an old mobile home’s frame to make both the pole and gib To make the underground swivel from the 3/4-ton pickup axle Bennett cut the axle off where it curves upward leaving the spindle and wheel hub intact He then welded 2 channel irons on top of the wheel hub one on each side of the hub and welded the axle kingpins solid so the spindle can’t turn Then he used a torch to sharpen the other end of the axle and used a heavy crowbar to drive it into the ground with the spindle and wheel hub facing up The gib pins onto a pair of channel irons welded to either side of the pole’s base He drilled 2 holes in each channel iron and bolted the pole and gib together He also welded on a pair of 1/4-in thick steel plates behind the channel irons for reinforcement The leftover part of the spindle including the wheel hub and bearing was mounted upside down on top of the pole to form a swivel point He cut off the lug nuts and then welded a steel plate to the hub cut holes in it and attached the guide wires “It works fantastic and has speeded up the entire log splitting process ” says Bennett “I built it last year and have already split 10 cords of wood with it I’ve used the gib to lift logs weighing up to 2 500 lbs although their average weight is closer to 1 500 lbs The guide wires are anchored to 2 large trees in my yard and to a rafter in the shed ” He says the system has other advantages “It’s a lot less labor intensive because I don’t have to carry the blocks or split wood very far Also I don’t risk running the saw’s chain down into the ground and ruining the chain ” Bennett needed something to safely raise the pole and set it in the ground so he used steel pipe to build a 12-ft long A-framed structure and chained it to his tractor’s front-end loader A pulley on the A-frame supports a cable with a loop that catches a corresponding tab welded onto the middle of the pole “My loader reaches about 20 ft high and the A-frame adds another 12 ft so I was able to get the pole upright and set it down into the underground swivel base ” notes Bennett Contact: FARM SHOW Followup Norman Bennett 188 Drown Mill Road Newport Vt 05855 ph 802 624-0720; bigtrukr@icloud com
To read the rest of this story, download this issue below or click
here to register with your account number.