2015 - Volume #39, Issue #1, Page #43
[ Sample Stories From This Issue | List of All Stories In This Issue | Print this story
| Read this issue]
Automated Worm Farm Ready For Market
![]() |
![]() |
![]() |
“We are looking for a partner to manufacture the worm farm,” says Meisel, a chemistry professor and greenhouse manager at the university. “We started work on this project about 5 years ago and settled on the final prototype about 3 years ago. It is designed to take up minimal space and do everything.”
The prototype weighs around 800 lbs. fully loaded and 350 to 400 lbs. when empty. Built from heavy tube frame to handle the weight, it is 60 in. long, 48 in. high and 30 in. wide. However, Meisel says it is size neutral and easily scaled up or down, whether for commercial operations or homeowners.
“Our prototype has sensors to check moisture content, and it adds water as needed,” says Meisel, who is also a part-time farmer. “It takes from 3 to 7 days to finish compost, depending on the material, and can be programmed accordingly.”
The worm farm consists of multiple components, including a shredder and contra-rotating cylinders. Material put through the shredder falls into the mouth of the inner cylinder where it is irrigated and aerated. Water is sprayed on the shredded material and air is pumped in while it goes through its first rotations. An established worm and microbial population in the cylinders goes to work on the material.
“We shred everything to give the microbes and worms the greatest possible surface area,” says Meisel. “The cylinders are painted black to absorb sunlight. The heat speeds the composting process and helps dry the material.”
The number of rotations the material goes through each day can be set by the operator and changed as needed. As more material is added and the cylinder is rotated, composting material is moved through the cylinder. When it reaches the end of the first cylinder, it falls into the second cylinder and repeats the process until the finished compost is expelled onto a screen.
The worms constantly migrate to fresh material, leaving finished vermicompost behind. Any material that doesn’t pass through the screen is simply run back through the shredder with that day’s fresh material and sent back through the process. Liquid waste or “worm tea” is drained off through the process and captured in a tank for daily harvest.
“We use the worm tea in our greenhouse and also sell it for about $8/gal.,” says Meisel. “It has lots of uses.”
Sprayed on the plants as a foliar fertilizer, it also protects the plants from pests. It can be sprayed on the soil to improve the soil and feed the plant roots. Meisel says they even add it to the water for campus beehives and have seen a reduction in mites.
“We use the vermicompost, which is full of worm castings, in the greenhouse as well,” says Meisel. “We get quicker germination, healthier plants with large roots and more blooms that last longer. We also have virtually no compacting in our greenhouse beds.”
Productivity of the unit depends on the type and quantity of bio-waste. In a recent test run, approximately 25 lbs. of waste added per day produced about 2 gal. of worm tea and about 2 1/2 lbs. of vermicompost daily.
Meisel says that 200 lbs. of worms will consume 100 lbs. of material per day. The university has also developed a worm separator. Excess worms are sold to area fishermen.
“The little red worms are preferred for bluegill and other pan fish,” he says.
Meisel is confident the automated worm farm is a success. The university has utilized various types of vermiculture-based composting for about 8 years.
The prototype cost about $2,000 to make. While the university is not interested in building machines, it is interested in marketing plans and finding a licensing partner.
“We haven’t used it much in the past few years as we were going through the patenting process,” says Meisel. “Once we filed for the provisional patent, we have had it working in the greenhouse, and a lot of people have shown interest.”
Contact: FARM SHOW Followup, Saginaw Valley State University, Center for Business and Economic Development, Harry Leaver, Executive Director, 7400 Bay Road, University Center, Mich. 48710 (ph 989 964-4047; hlleaver@svsu.edu; cbed@svsu.edu).
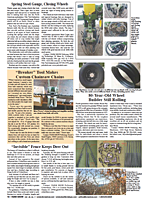
Click here to download page story appeared in.
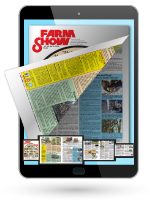
Click here to read entire issue
To read the rest of this story, download this issue below or click here to register with your account number.