You have reached your limit of 3 free stories. A story preview is shown instead.
To view more stories
(If your subscription is current,
click here to Login or Register.)
Problem Parts Custom-Molded In Poly
If you have a part that continually wears out, Rob Cerne, Seascape Technologies, may have what you need. He says he can often make a replacement part that is better than the original. Seascape molds polyurethane specifically selected to solve problems that made the original parts fail.
“Our polyurethane is spec
..........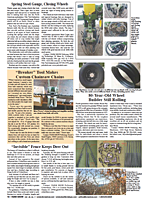
You must sign in, subscribe or renew to see the page.
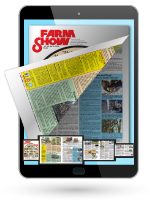
You must sign in, subscribe or renew to see the flip-book
Problem Parts Custom-Molded In Poly SPECIALTY/SERVICES If you have a part that continually wears out Rob Cerne Seascape Technologies may have what you need He says he can often make a replacement part that is better than the original Seascape molds polyurethane specifically selected to solve problems that made the original parts fail “Our polyurethane is specially formulated for the intended use ” says Cerne “It can be as soft as chewing gum as hard as carbide and bend in a thousand different ways springing back to the original shape There is one formula that can go in a 300° oven and not be affected Seascape looks at the problem that caused the part to fail and finds the right formula Pricing is based on material used labor volume and complexity of the product to be produced The company has the expertise to form molds from an existing part a print or a sketch Customers send us pictures of the part or the part itself and tell us why the part failed whether friction heat moisture or abrasion says Cerne We ask questions then sit back and listen He says Seascape works with some of the largest foundries in the country as well as small independent shops and individual orders The company makes tank liners machinery wheels rollers seals wipers and wear parts for use in mining manufacturing agriculture and foundry operations In many cases Seascape may already have a mold or even a needed part About 80 percent of sales are for universal parts and 20 percent for custom Cerne says that even a single order can be worth it Often a custom-made part leads us to other people who have the same equipment and need the part as well says Cerne We make wheels for Deere deck mowers that are better than the original rubber ones If you’re changing deck wheels every spring we ll send you ones that won t wear so fast Custom molds can be machined on a lathe or polyurethane may be used to make special tooling or molds Doing all tooling in-house lets Seascape keep its costs down notes Cerne So far there is no limit to the size of the product we can make says Cerne Our job is to solve problems for people and make their days easier Contact: FARM SHOW Followup Seascape Technologies N5230 Hwy E Ogdensburg Wis 54962 ph 920 244-7767; seascape@wolfnet net; www seascapetechnologies com
To read the rest of this story, download this issue below or click
here to register with your account number.