You have reached your limit of 3 free stories. A story preview is shown instead.
To view more stories
(If your subscription is current,
click here to Login or Register.)
Using Natural Gas In Diesel Engines
A growing number of irrigation farmers are realizing substantial savings by converting diesel irrigation pumps to natural gas. Nebraska farmers Jerl Joseph and his son Eric saved hundreds of dollars a year in fuel costs after they converted two diesel-burning irrigation-pump engines to natural gas. One of them is a Ca
..........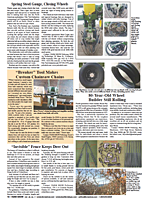
You must sign in, subscribe or renew to see the page.
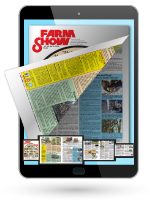
You must sign in, subscribe or renew to see the flip-book
Using Natural Gas In Diesel Engines ENERGY Alternative Fuels A growing number of irrigation farmers are realizing substantial savings by converting diesel irrigation pumps to natural gas Nebraska farmers Jerl Joseph and his son Eric saved hundreds of dollars a year in fuel costs after they converted two diesel-burning irrigation-pump engines to natural gas One of them is a Case-IH 4-cylinder that runs a quarter section pivot plus an additional 40 acres The other is a 4-cylinder Deere on an 80-acre pivot After converting the engines with a kit the Joseph’s plumbed the engines for the natural gas feed Until recently Norman Bredthauer of Arcadia Neb had the longest pivot irrigator in Valley County and the engine powering it consumed 7 5 gal /hr of diesel fuel Norman’s fuel bill was $30 000/year for this one engine After he converted to natural gas Bredthauer’s engine was using gas at a rate of 7 25 therm/hr There are approximately 1 4 therm in a diesel gallon equivalent which meant that this engine now uses the equivalent of 5 2 gal /hr of diesel fuel with natural gas The conversion therefore reduced Bredthauer’s operating costs from $28 13/hr figuring diesel fuel at $3 75/gallon to about $13 64/hr a savings of $14 49/hr The Nebraska farmers converted the engines with kits from C&E Clean Energy Solutions in Sturgis S Dak The kits included the required gas valves and solenoid a fuel-injection manifold that fit between the air intake and the turbocharger and a pyrometer temperature gauge that was installed in the exhaust manifold to protect against overheating The kit meters natural gas into the engine airstream after the engine is started using diesel Joseph says it generally costs about half as much to irrigate using natural gas He adds that the best part of the conversion is that you can go back to 100 percent diesel at any time He says kits are sized for engine horsepower and fuel consumption A kit ranges from about $1 300 for engines up to 75 hp to $3 400 for larger engines Joseph says if diesel becomes less expensive than natural gas or the flow of natural gas is interrupted he can easily go back to diesel According to C&E return-on-investment on a stationary diesel application can be achieved in a few hundred hours of operation The kits work well on both turbocharged and naturally aspirated stationary engines Contact: FARM SHOW Followup C&E Clean Energy Solutions Sturgis S Dak 57785 ph 800 435-6810; info@cecleanenergy net; www cecleanenergy net
To read the rest of this story, download this issue below or click
here to register with your account number.