You have reached your limit of 3 free stories. A story preview is shown instead.
To view more stories
(If your subscription is current,
click here to Login or Register.)
“Made It Myself” Truck Axle Composter
Sonoma grape farmer Paul Bernier of Geyserville, Calif., built a 3-pt. mounted compost turner using a 20,000-lb. truck differential. He uses the compost turner on windrows that are 12 ft. wide, 120 ft. long, and spaced 8 ft. apart.
“It’s a cost-effective way of turning grape compost, or ‘pomace’, which I us
..........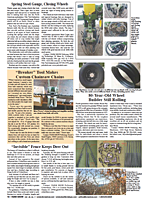
You must sign in, subscribe or renew to see the page.
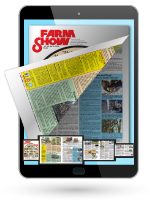
You must sign in, subscribe or renew to see the flip-book
“Made It Myself” Truck Axle Composter MISCELLANEOUS EQUIPMENT Miscellaneous Sonoma grape farmer Paul Bernier of Geyserville Calif built a 3-pt mounted compost turner using a 20 000-lb truck differential He uses the compost turner on windrows that are 12 ft wide 120 ft long and spaced 8 ft apart “It’s a cost-effective way of turning grape compost or ‘pomace’ which I use to improve the organic matter in the soil around my vineyard ” says Bernier “The machine is only 6 1/2 ft wide so there’s plenty of room to maneuver between windrows It lets us pack a lot of windrows into a relatively tight space The windrows are made up of both stems and pomace from a local vineyard press We’re composting the material into a mixture that breaks down easily and is also easier to apply with a spreader ” Bernier says he has been making compost for his operation for more than 35 years in the past turning it with a loader tractor “The loader did an adequate job but it was slow and took up a lot of space I borrowed a friend’s commercial compost turner one year but I didn’t like the machine’s 7 000-lb weight or the 100 hp tractor required to operate it “I thought if I only turned half the width of the windrow at a time I might be able to use my 70 hp 2-WD wheel tractor to pull a much smaller machine And I’d be saving money Commercial compost turners sell for about $25 000 or more whereas I spent only about $1 000 It took me about a month to build ” He copied the specs of the commercial turner to build his own machine It’s equipped with a 16-in dia drum fitted with 8-in paddles which rotate against the direction of travel at about 200 rpm’s “I thought a truck differential would do the job of a right angle drive and found a 20 000-lb broken axle in a friend’s scrap bin ” says Bernier “The axle was geared a little low at 5 28:1 but my tractor has a 2-speed pto which results in about 200 rpm’s at the end of the axle I had to mount the housing upside down to get the correct rotation I cut off the unneeded axle tube welded the spider gears to the cage to eliminate differential action and carefully aligned everything so that it runs true ” The agitator drum is made from 3/16-in thick by a length of 16-in dia well casing which Bernier welded to a 10-hole bud wheel center “I removed the brakes and backing plate from the axle tube but kept the wheel hub which the agitator drum is fastened to with lug nuts The agitator is 6 1/2 ft long so it’ll easily turn a 12-ft windrow I go down one side of the windrow then turn around and come back down the other side “I’ve used the machine for 5 years and turned more than 10 000 yards of compost with no problems Truck rear ends are built tough ” Bernier used 1/2-in thick flat stock to build the tines and bolted them onto brackets that are welded to the drum A home-built angled steel blade runs alongside the tractor to lift up compost material just before it’s turned A length of truck tire tread bolted to a metal plate serves as a deflector at one end of the drum to keep material from being thrown back at the driver “Anyone with high school shop skills and access to a junkyard could build a compost turner like mine ” notes Bernier Contact: FARM SHOW Followup Paul Bernier 1720 Canyon Rd Geyserville Calif 95441 ph 707 849-7620; lreinreb@gmail com
To read the rest of this story, download this issue below or click
here to register with your account number.