“Car Part” Walker Gets Livestock In Shape
Commercial walkers for getting show animals in shape can cost more than $10,000 so Mike Rising built his own. So far he has used it successfully with horses, steers, sheep and goats, keeping them in shape for livestock shows. Made with a car transmission for the drive unit, he can alter the speed and the direction as needed.
“The walker is designed to handle 4 animals at a time in separate compartments, but we prefer to use only 2,” says Rising. “This gives the animals the opportunity to turn or stop for a brief time depending on what gear you are in.”
At the center of the walker, Rising mounted a car rear end with one axle stub mounted to a metal frame on a concrete pad. The other axle serves as the base for the 4 moving (26-ft. long) arms that “walk” the animals. A 4-in. diameter pipe attached to the axle stub reduces down, first to 3-in. and again to 2-in. The arms, which extend up and out from the base of the 4-in. pipe, are supported by steel straps that lead back to the 3-in. pipe and cable that runs from about 10 ft. from the ends of the arms, back to the top of the 2-in. pipe.
“The cable really makes a difference stabilizing the arms,” says Rising.
Lengths of 1/2-in. sucker rod connect and stabilize the arms at about 8 ft. from the center. They maintain a common distance between the arms.
The arms rotate around 2 rings of livestock panels spaced about 10 ft. apart. The outer ring has sixteen, 10-ft. panels and a 4-ft. bow gate for access. The inner ring consists of nine, 10-ft. panels with a 4-ft. bow gate for access.
Rising hangs 10-ft. panels on 1/2-in. steel tubing hinged at the top to two opposing arms. As the arms move around the ring, the animals are encouraged to move by the panels pushing them forward. However, should an animal get in trouble or simply stop, the hinged panel will ride up and over them.
To drive the arms and panels, Rising attached a 3-speed transmission to the side of the rear end. A belt drive on one end of the transmission is powered by an 850-rpm electric motor. At the other end of the transmission, a second belt drive transfers power to the driveshaft on the differential. An off/on switch mounted outside the walker lets Rising control power once the speed has been selected.
“It’s hard to estimate how much the walker cost as I had all the parts on hand,” says Rising. “The rear end, the transmission and the pipe were all used. The livestock panels were the most expensive, but the lane could have been made out of wood to defray the cost.”
Contact: FARM SHOW Followup, Michael Rising, P.O. Box 65, Nutrioso, Arizona 85932 (ph 928 339-4349).
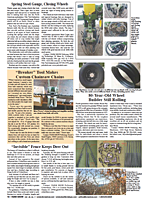
Click here to download page story appeared in.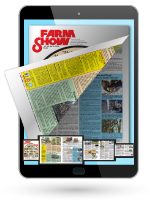
Click here to read entire issue
“Car Part” Walker Gets Livestock In Shape LIVESTOCK Horses/Mules Commercial walkers for getting show animals in shape can cost more than $10 000 so Mike Rising built his own So far he has used it successfully with horses steers sheep and goats keeping them in shape for livestock shows Made with a car transmission for the drive unit he can alter the speed and the direction as needed “The walker is designed to handle 4 animals at a time in separate compartments but we prefer to use only 2 ” says Rising “This gives the animals the opportunity to turn or stop for a brief time depending on what gear you are in ” At the center of the walker Rising mounted a car rear end with one axle stub mounted to a metal frame on a concrete pad The other axle serves as the base for the 4 moving 26-ft long arms that “walk” the animals A 4-in diameter pipe attached to the axle stub reduces down first to 3-in and again to 2-in The arms which extend up and out from the base of the 4-in pipe are supported by steel straps that lead back to the 3-in pipe and cable that runs from about 10 ft from the ends of the arms back to the top of the 2-in pipe “The cable really makes a difference stabilizing the arms ” says Rising Lengths of 1/2-in sucker rod connect and stabilize the arms at about 8 ft from the center They maintain a common distance between the arms The arms rotate around 2 rings of livestock panels spaced about 10 ft apart The outer ring has sixteen 10-ft panels and a 4-ft bow gate for access The inner ring consists of nine 10-ft panels with a 4-ft bow gate for access Rising hangs 10-ft panels on 1/2-in steel tubing hinged at the top to two opposing arms As the arms move around the ring the animals are encouraged to move by the panels pushing them forward However should an animal get in trouble or simply stop the hinged panel will ride up and over them To drive the arms and panels Rising attached a 3-speed transmission to the side of the rear end A belt drive on one end of the transmission is powered by an 850-rpm electric motor At the other end of the transmission a second belt drive transfers power to the driveshaft on the differential An off/on switch mounted outside the walker lets Rising control power once the speed has been selected “It’s hard to estimate how much the walker cost as I had all the parts on hand ” says Rising “The rear end the transmission and the pipe were all used The livestock panels were the most expensive but the lane could have been made out of wood to defray the cost ” Contact: FARM SHOW Followup Michael Rising P O Box 65 Nutrioso Arizona 85932 ph 928 339-4349