Students Built Loader-Mounted Hay Forks From Scratch
“My son and I recently built this set of hay forks for a Deere front-end loader with a local high school boy, as part of an Ag Mechanics project for a local Future Farmers of America. It has been patented and we’d like to get it in front of some people who can appreciate it and use it,” says Gary Machado, Carrollton, Texas.
The 4-ft. long forks are built from 2 5/8-in. dia. cold rolled steel and are designed to slide in or out by means of a 16-in. long, 3-in. dia. hydraulic cylinder attached to a telescoping tube. As a result, the forks can handle round bales ranging from 4 to 5 ft. wide.
The telescoping tube is bolted to a frame with quick tach brackets welded on back of it. The width between forks is set by inserting a pin into a hole.
“The operator can insert the forks into the bale, or grasp it from both sides to keep from damaging net-wrapped bales,” says Machado. “The design lets you stack bales either on their ends or on their sides.”
Machado says they built the hay forks in his small shop “which doesn’t have a lot of high tech fancy equipment”, and made all components, including the telescoping attachment and frame, from scratch.
“To build the frame we started with 1/4-in. thick steel plate and had the pieces custom cut to different lengths, which we then welded together. I tried to teach the kids how to take measurements accurately, and clean up the plates and get them ready to weld together.”
He says the hardest part was building the telescoping attachment. “The larger tube is built from 1/2-in. thick wall material and came with a seam inside it, which we had to remove in order for the smaller tube to fit.”
To solve the problem, they duct taped an air-operated die grinder, along with the air hose attached to it, to a broom handle and then stuck the grinder inside the pipe. They zip tied the grinder’s handle open to keep the grinder running constantly.
“The operator had to use a face shield to keep flying sparks off him,” says Machado. “My son ‘throttled’ the compressor by controlling the amount of kink in the air hose. It took a few hours to totally remove the seam.”
Machado adds that his friend Ed Stanley was a major partner and now owns the project.
Contact: FARM SHOW Followup, Gary Machado, 2111 Sequoyah Way, Carrollton, Texas 75006 (ph 469 853-8678; gmachado13@verizon.net).
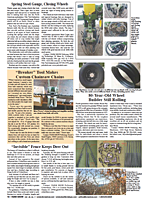
Click here to download page story appeared in.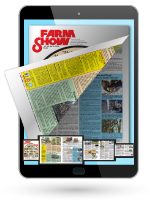
Click here to read entire issue
Students Built Loader-Mounted Hay Forks From Scratch BALE HANDLING “My son and I recently built this set of hay forks for a Deere front-end loader with a local high school boy as part of an Ag Mechanics project for a local Future Farmers of America It has been patented and we’d like to get it in front of some people who can appreciate it and use it ” says Gary Machado Carrollton Texas The 4-ft long forks are built from 2 5/8-in dia cold rolled steel and are designed to slide in or out by means of a 16-in long 3-in dia hydraulic cylinder attached to a telescoping tube As a result the forks can handle round bales ranging from 4 to 5 ft wide The telescoping tube is bolted to a frame with quick tach brackets welded on back of it The width between forks is set by inserting a pin into a hole “The operator can insert the forks into the bale or grasp it from both sides to keep from damaging net-wrapped bales ” says Machado “The design lets you stack bales either on their ends or on their sides ” Machado says they built the hay forks in his small shop “which doesn’t have a lot of high tech fancy equipment” and made all components including the telescoping attachment and frame from scratch “To build the frame we started with 1/4-in thick steel plate and had the pieces custom cut to different lengths which we then welded together I tried to teach the kids how to take measurements accurately and clean up the plates and get them ready to weld together ” He says the hardest part was building the telescoping attachment “The larger tube is built from 1/2-in thick wall material and came with a seam inside it which we had to remove in order for the smaller tube to fit ” To solve the problem they duct taped an air-operated die grinder along with the air hose attached to it to a broom handle and then stuck the grinder inside the pipe They zip tied the grinder’s handle open to keep the grinder running constantly “The operator had to use a face shield to keep flying sparks off him ” says Machado “My son ‘throttled’ the compressor by controlling the amount of kink in the air hose It took a few hours to totally remove the seam ” Machado adds that his friend Ed Stanley was a major partner and now owns the project Contact: FARM SHOW Followup Gary Machado 2111 Sequoyah Way Carrollton Texas 75006 ph 469 853-8678; gmachado13@verizon net
To read the rest of this story, download this issue below or click
here to register with your account number.