You have reached your limit of 3 free stories. A story preview is shown instead.
To view more stories
(If your subscription is current,
click here to Login or Register.)
Grain Cleaner Has No Moving Parts
"My home-built grain cleaner has no moving parts and cost only $200 to build not counting augers," says Gerald Ochsner, Sutton, Neb., who mounted a 9-ft. long, 12-in. wide grain cleaning screen on a 20-ft. long 6-in. dia. auger that feeds grain from his 580 bu. dump pit into a 50,000-bu. quonset building and three 15,0
..........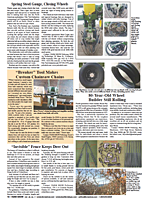
You must sign in, subscribe or renew to see the page.
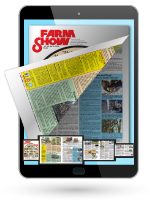
You must sign in, subscribe or renew to see the flip-book
Grain Cleaner Has No Moving Parts GRAIN CLEANERS Grain Cleaners (29C) 14-2-7 "My home-built grain cleaner has no moving parts and cost only $200 to build not counting augers," says Gerald Ochsner, Sutton, Neb., who mounted a 9-ft. long, 12-in. wide grain cleaning screen on a 20-ft. long 6-in. dia. auger that feeds grain from his 580 bu. dump pit into a 50,000-bu. quonset building and three 15,000 bu. drying bins.
The cleaning screen, made of high car-bon steel with 1/4-in. dia. openings, was designed to wash gravel in gravel mining pits. Ochsner bought it from a foundry that rebuilds gravel pit pumps. The 9-ft. long screen is enclosed within an open-top 10-ft. long steel frame that's attached to the bottom side of the upper end of the auger. The auger, which runs diagonally toward the top of the quonset, dumps grain onto the top end of the screen. Grain flows by gravity down over the length of the screen and the fines drop out through a flexible pipe and into a wagon. Clean grain is picked up at the bottom end of the screen by a second auger that delivers it to the top of the 19-ft. high quonset.
"I use in-bin natural air to dry my corn in layers," says Ochsner, who built the grain cleaner 14 years ago. "The cleaner the grain, the more efficiently it dries. My auger-mounted screen always delivers no. 1 or 2 grade com with no dockage. Rotary cleaners cost up to $3,000 and require cumbersome electric motors and augers. I wanted something permanent and simple without any moving parts. The 12-ga. steel frame that encloses the screen keeps the wind from blowing fines across the yard so there's no mess to clean up after-ward. I've already run 300,000 bu. of corn through the cleaner and I think it'll handle another 300,000 bu."
Ochsner paid $10 per foot for the screen which he bought in a 36 in. wide roll and cut to a 12-in. width. He used metal staples to attach the screen to a 1-in. wood frame. The screen lays on top of 3 1/4-in. bolts set into the steel frame. "Several neighbors have copied my grain cleaner idea and use 18-in. wide screens that handle up to 3,000 bu. per hour. They mount the screens on the sides of grain storage buildings or inside the bin under the roof."
Contact: FARM SHOW Followup, Gerald Ochsner, RR 2, Box 3B, Sutton, Neb. 68979 (ph 402 773-5216).
To read the rest of this story, download this issue below or click
here to register with your account number.