1982 - Volume #6, Issue #6, Page #21
[ Sample Stories From This Issue | List of All Stories In This Issue | Print this story
| Read this issue]
Hog Barn Built With Straw Bales
![]() |
Leussink used right at 1,000 square bales (4 by 4 by 7 ft.) made with a Hesston big baler to build this 430 ft. by 40 ft. barn and a 36 by 100 ft. annex. Individual bales were compressed with 2,500 lbs. of pressure and tied with six strands of twine.
The T-shaped structure, with about 20,000 total sq. ft. of floor space, houses his entire breeding, farrowing, and finishing operation. He markets about 7,000 hogs a year.
Side walls of the barn are two bales high (8 ft.)-and 4 ft. thick. Inside the barn, pens are built of poured concrete 3 in. thick and 42 in. high, which keeps the pigs completely out of contact with the straw walls. The concrete pen walls also provide a support on which to bolt roof supports.
Pine poles are placed over the steel roof supports, then covered with 6 mil plastic. Over this is a 3 ft. slice from a big straw bale, another sheet of plastic, and a foot of loose straw.
Leussink thinks the roof will have to be replaced in five years but the walls "will last forever".
"The building sheds water and the walls never stay wet," he says. "Temperature stays up around 70? in winter, and there's never any moisture on the inside walls and ceiling in cold weather."
The building is ventilated by six thermostatically-controlled fans that are fitted into steel cages set in the straw wall. All the lighting and electrical wires are hung from the ceiling completely clear of the walls and ceiling.
Leussink says there is no combustible material near the electrical wiring, and he doesn't consider the barn to be a fire hazard, but he can't get it insured. "My old conventional hog barn is more vulnerable to fire than this one," he notes.
He built the whole set-up for less than $80,000, and about $30,000 of that is for the feeding systems alone. The concrete work was $18,000. A comparable size conventional hog barn would have cost 10 to 12 times as much, says Leussink.
He grew up in the Netherlands where straw thatched roofs are still found, so he knows the good points about them. He had to make a lot of modifications and had to come up with some inventive ideas. The roof supports and concrete pens are his own ideas. So is the manure handling system, which works by gravity.
The straw barn is so successful that another one is being built by Leussink, and still another by his son. The Leussinks are learning by experience how to improve this kind of building.
"Flax straw is probably the best all-around for building, and rye straw is the toughest," says Leussink. The straw walls harbor mice but the rodent problem has been no worse than with a conventional barn, he points out.
"The big advantage of the straw barn is the good shelter it provides at low, low cost. It's the way to go if you want to make a few bucks on your livestock operation," Leussink concludes. "If a straw bale starts rotting for any reason, it can be removed and a new one put in its place."
For more information, contact: FARM SHOW Followup, George Leussink, Box 451, Sundre, Alberta (ph 403 638-3863).
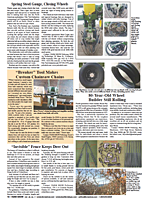
Click here to download page story appeared in.
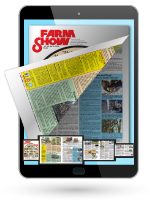
Click here to read entire issue
To read the rest of this story, download this issue below or click here to register with your account number.