You have reached your limit of 3 free stories. A story preview is shown instead.
To view more stories
(If your subscription is current,
click here to Login or Register.)
4WD Loader Built For Cattle Feeding
Conventional farm tractors aren't built for heavy-duty loader work around a feedlot, in the opinion of Alberta farmer Doug Lansdell who decided to build his own 4-WD loader tractor because he couldn't fmd a commercial machine he liked.
"We didn't like the durability and capacity of tractor loaders.The biggest pr
..........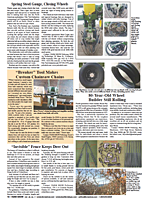
You must sign in, subscribe or renew to see the page.
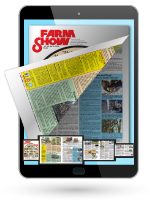
You must sign in, subscribe or renew to see the flip-book
4WD loader built for cattle feeding TRACTORS Loaders 13-6-21 Conventional farm tractors aren't built for heavy-duty loader work around a feedlot, in the opinion of Alberta farmer Doug Lansdell who decided to build his own 4-WD loader tractor because he couldn't fmd a commercial machine he liked.
"We didn't like the durability and capacity of tractor loaders.The biggest problem is that the load is carried on the front axle. We also had trouble every spring when we needed our tractors for fieldwork but still had to use them to feed cattle. We finally built our own loader," says Lansdell.
"We started with a 4-WD surplus government snowplow made in the 1940's or early 50's. We stripped it down to the frame, getting rid of all power train components except for the rear ends. Next, we bought a junked Case 1000D crawler tractor for the loader and mounted it on the truck frame with the steering axle at the rear. We had to cut the truck frame to lower it down to mount directly on the axle so the loader would be the right distance from the ground. We installed a big transfer case from another 4-WD truck and shortened up the wheelbase to make the machine as maneuverable as possible. The shortest we could go was 9 ft. because of the large differentials and transfer case. If possible, it would be better to shorten it up to 8 ft.
"The next step was to find a way to make the machine run backwards and to slow it down. We finally came up with the idea of cutting an old truck 5-speed transmission apart and to use the clutch shaft and the first gear on the counter shaft. We ended up cutting 8 1/2 in. outof the transmission case and welding it back together. The clutch shaft had a stub welded in the pocket bearing hole and was turned to fit the original rear shaft bearing. We built a new counter¡shaft to extend out the rear through the hole bored in the lower countershaft bearing cap. The cab was bored to fit a seal. From there we went to an automatic transmission from a 1972 Chevrolet 1/2-ton and a 25O cu. in. 6¡cyl. Chevrolet engine. We used the radiator housing from the Case dozer because it's heavy enough to act as a counter-weight. A shaft was made up to connect to the front crankshaft pulley and acts as a drive for the air compressor, fan and hydraulic pump.
"We needed at least 30 gpm hydraulics for a loader this size. We got a heavy-duty 3-spool valve from a tractor wrecker. The original truck steering ram was used. We simply installed a steering box from a Chevrolet car and connected it up. The cab was salvaged from an old tractor. The last major project was to build a bucket and a grapple fork. We had an 8-ft. long sheet of steel 5/16 in. thick formed at a welding and fabrication shop. Then we built the grapple fork to be big enough to handle two large bales at once even if they are poorly tied.
"The finished machine easily handles two bales at a time, which saves a lot of time when feeding and when unloading trucks. It cost about $5,000 and took about a year of spare time to build. The project probably wouldn't have been possible without the lathe and other tools in our farm workshop."
Contact: FARM SHOW Followup, Doug Lansdell, Box 119, Turner Valley, Alberta TOL 2A0 Canada
To read the rest of this story, download this issue below or click
here to register with your account number.