2015 - Volume #39, Issue #6, Page #20
[ Sample Stories From This Issue | List of All Stories In This Issue | Print this story
| Read this issue]
High-Capacity Gravity Box Cattle Feeder
![]() |
![]() |
“Larger cattle will often push younger ones away from the feed,” notes Burlage. “The great thing about this feeder is that if a bigger steer is eating on one side, he can’t see the smaller steer on the other side.”
Burlage has fed cattle for years, starting 10 head or so at a time every 3 months or so. The scheduling guarantees he always has some on hand that are ready for the butcher. Burlage sells most of his cattle to individuals as locker meat.
With a full-time job off the farm, he got tired of transferring feed from a bulk bin to the hog feeders he used. Having delivered feed for several years, he'd seen a lot of setups, so he knew what worked and what didn’t.
“I noticed that with most V-shaped, commercial cattle feeders, the animal would stand at an angle, take a mouth full of feed, and then turn away from the feeder and eat,” says Burlage. “Feed would drop on the feedlot floor and go to waste.”
Burlage wanted a feeder big enough to handle a delivery once a month. When Burlage’s father pointed out two center dump gravity boxes for sale in the neighborhood, he started to work on the design. With the help of his son, a top-notch welder, he cut holes out of each side and fabricated a push plate that lets the cattle knock down feed. He also installed a wedge-shaped block on the floor of the wagon so that feed would drop evenly to all four sides.
He also designed it so cattle would stand head-on. That way, dropped feed would go back into the bunk. His feeder design includes plastic-lined bunks so calves can push their feed around and the bunks are easy to clean.
“My son welded 4-in. channel iron supports for a 2 by 6, tongue and groove, wood bunk floor about 20 in. above the ground,” says Burlage. “Bunk sides are 2 by 10s. We also used channel iron and some other steel to make six 80-in. legs that we bolted to the sides of the wagon box.”
Burlage made gussets from 4-in. wide, 3/16-in. steel to go from the stilts to the channel iron floor supports.
The roof was framed with 3-in. galvanized angle iron edges and 16-ft. 2 by 4s spaced 2 ft. apart for joists. These were overlaid with 3/8-in. plywood, a layer of Tyvek, and galvanized tin roofing material.
“My brother installs HVAC equipment, so he bent the tin for the roof,” says Burlage. “I screwed it down. Everything on the feeder is either screwed or bolted together.”
To increase feed storage capacity, Burlage offset the roof panels. Instead of equal sizes, the fixed position panel is 45 percent of the roof area. The 55 percent panel tips to the side.
“I wanted the auger over the larger panel for a bigger fill,” says Burlage.
The roof panels are also significantly larger than the underlying bunk area. All four sides extend out over the bunk to protect it from all but a driving rain or snow.
To make it easier to tip the panel open, Burlage hung cinder block counterweights on the lower corners, balancing the panel and making it easy to pull it back into place with cables attached to the top corners of the roof panel. Once in place, the cables slip over tie-down hooks to secure the panel in place.
Moving the feeder up the hill from where it was made would have been difficult without salvaged I-beams from an old concrete corncrib. The I-beams were just the right size to slip under the stilts. Welded in place, they made first-rate runners.
“We slid it right up the road and into place on the feeding floor,” recalls Burlage. “The feeder holds 8 tons of feed, and my cattle are dressing out better than with the old hog feeders I used before.”
Contact: FARM SHOW Followup, Mark Burlage, 11743 318th Ave., Kinross, Iowa 52335 (ph 319-639-2666).
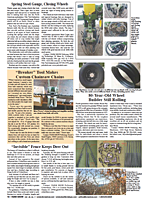
Click here to download page story appeared in.
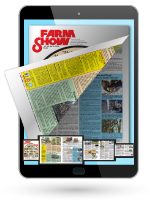
Click here to read entire issue
To read the rest of this story, download this issue below or click here to register with your account number.