2015 - Volume #39, Issue #6, Page #40
[ Sample Stories From This Issue | List of All Stories In This Issue | Print this story
| Read this issue]
No-Heat System Dries Grain Without Damage
![]() |
![]() |
“It’s competitive with natural gas and much better than propane,” says Dave Loebach. “Since we don’t raise the temperature, we don’t affect germination or get cracks from heat.”
“Drying time is not comparable to a heat-based dryer,” acknowledges Joe Loebach. “It may take 2 to 3 months in a 30,000-bushel bin. We’re aiming this at guys who were going to put air through their bin anyway. This lets them bring down moisture in the storage bin.”
The closed loop system includes several novel aspects. Once a bin is filled, nitrogen or carbon dioxide is added to push the oxygen out, and the bin is sealed. This prevents spoilage as the grain dries. It is this oxygen-deprived air that is circulated through the drying mechanism at ambient temperatures, pulling moisture out of the grain with every pass.
The drying mechanism is a 2-coil system, with one coil acting as a condenser and the other coil acting as an evaporator. Moist air from the top of the bin is pulled through both coils. As the temperature of the condenser coil drops to 11 degrees below zero, moisture from the air condenses on the inside of the coil, drying the air, which then passes back to the grain. When the coil has filled with ice, its temperature is allowed to rise. At the same time, the second coil is cooled. While ice in the first coil melts and moisture drains out of the system, the second coil is pulling moisture from the air.
“We can keep it running continuously, switching back and forth between the 2 coils,” says Dave. “Although we are only drying half the air being drawn through the system at a time, we can use ambient air. That means we can dry grain whether it is at 70 degrees or zero.”
Dave Loebach, who lives in Idaho, actually got the idea for the system after training as a refrigeration specialist. Throughout his 40-year career, he periodically considered how the system could work. Dave would talk it over with brother Joe, who farmed in Iowa. Over the years both set aside parts they thought might work.
“My wife finally told me to build the thing or clean out the garage,” says Dave.
Dave contributed a twin-flow evaporator, a compressor, reversing valve, condenser, expansion valves, a timer and a blower. Joe contributed electrical components, a 70-year-old flare box wagon, a grain floor from a drying bin, and a doorbell transformer.
The rough prototype the two put together in 2012 is a wagon box-sized system. They put the dryer floor in the bottom of the flare box wagon and a tarp over the top to seal it. The blower cycled the air through the system and a load of 23 percent corn dried down to 15 percent in only 3 days. Even better, they used a 12 kW wind generator to power the system. This is something they feel others could do as well, further reducing costs.
“We showed it to several seed corn companies with proof of germination quality, but there was limited interest,” says Dave. “We’ve had some interest from a bin manufacturer, and now Iowa State is evaluating it.”
University engineers working with the Loebach brothers’ prototype were not prepared for how well it worked. “The first test started with 25 percent corn, and the researcher didn’t check it often enough. It dried down to 12 percent,” recalls Joe. “He said, ‘This will work.’
“We’re continuing to work on reducing costs and finding a company to commercialize it.”
Contact: FARM SHOW Followup, Loebach Brothers Moisture Removal System, P.O. Box 916, Nampa, Idaho 83653 (ph 208 697-7777; jloebachklein@netins.net; sailboatcw@gmail.com).
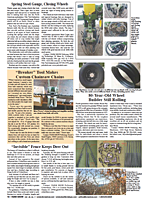
Click here to download page story appeared in.
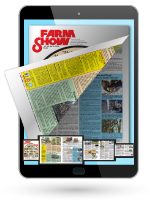
Click here to read entire issue
To read the rest of this story, download this issue below or click here to register with your account number.