2016 - Volume #40, Issue #1, Page #38
[ Sample Stories From This Issue | List of All Stories In This Issue | Print this story
| Read this issue]
“Single Pour” Floor Eliminates Need For Separate Foundation
![]() |
![]() |
“It was a lot cheaper than a traditional foundation,” says Eby. “A standard pole shed would have been a little less initially, but when I go to insulate and finish out the interior, I’ll be money ahead.”
Eby’s plans for the 24 by 36-ft. workshop included an insulated slab with in-floor heat. He sloped the ground so the outside three feet of the slab would be 6 in. thick and the interior 4 in. thick.
“We drilled 15-in. dia. holes, 42 in. deep, every 6 1/2 ft. around the load bearing sides of the slab,” says Eby. “Holes at either end, which only support the walls and not the roof or snow load, were spaced every 8 ft.”
A uniform 2-in. thick layer of foam insulation was laid down with PEX waterline, floor drain and rebar laid out above the foam. Three pieces of rebar were placed in corner holes with right angle bends at about a 46-in. height. Two rebars with similar right angle bends were inserted into the remaining holes.
Two pieces of rebar also passed over each hole. The top legs of the bent rebar were tied into surrounding rebar. These further reinforced the connection between the concrete slab and the in-ground columns after the concrete was poured.
Once the concrete cured, Eby put up the stick-built structure. About half the materials were recycled at little or no cost.
“I picked up fiber cement siding at a farm sale for pennies on the dollar,” says Eby. “The total cost was about $7,000 compared to about $30,000 with all new.”
Contact: FARM SHOW Followup, Matt Eby, 56641 Glenwood Rd., Cassopolis, Mich. 49031 (ebyfarmsllc@gmail.com).
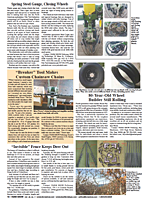
Click here to download page story appeared in.
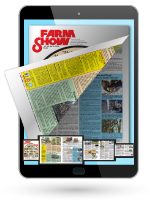
Click here to read entire issue
To read the rest of this story, download this issue below or click here to register with your account number.