2016 - Volume #40, Issue #3, Page #23
[ Sample Stories From This Issue | List of All Stories In This Issue | Print this story
| Read this issue]
Tractor Converted To Remote Control
![]() |
![]() |
![]() |
![]() |
“I did the conversion on my Deere 4210,” says Laine. “The hydrostatic drive and power steering helped keep the project manageable. It eliminated the need for throttle control, as the hydrostatic lets you control speed with a constant throttle setting. All I had to do was control fore and aft direction, speed and steering.”
Laine used a standard RC controller from Futaba that’s used on RC cars. The receiver that mounts to the tractor has a range of about 500 ft. and cost about $70.
“I needed to convert signals from the RC receiver into outputs at the tractor,” says Laine.
This required that he piggyback electrical controls to the hydrostat and mechanical controls to the steering column. Foot pedals on the 4210 are equipped with position sensors that feed signals to the engine control unit. Laine spliced into the wires for power, ground, and fore/aft signals.
The added wires were connected to an electronics control module Laine designed to read output signals from the transmitter. Unless the hand held transmitter is turned on, the tractor operates normally. When turned on, the electronics module uses its signals to imitate foot pedal-activated signals.
As the steering is hydraulically controlled, he needed a way to motorize the steering shaft for RC, but be able to disconnect the motor for manual control.
“I found a used 12V DC motor with electric clutch on eBay for $35,” recalls Laine. “The motor was too slow, but the clutch, which normally sells for around $200, could be repurposed.”
Laine attached a stepper motor with gear reduction to the clutch, attaching it in turn to a chain drive. He made adapters for both to mount them to the tractor and mounted a sprocket on the steering shaft. A #25 roller chain connects the chain drive on the clutch with the shaft. Signals received by the module are directed to the motor and the clutch for either remote control of the shaft or to disengage the clutch for manual control.
“The microprocessor and stepper motor electronics driver module fit in a stout metal box for physical and electronic protection and are mounted under the instrument panel,” says Laine. “I did have to give up the tilt-steering function to make room for the motor, but I hadn’t used it in the previous 15 years that I had the tractor.”
Laine admits that the process was filled with challenges, including just getting the steering wheel off. He ended up cutting it off and replacing it. The hydrostat control box had to be redone to be more mechanically and electrically robust.
“The steering mechanical was the biggest issue,” says Laine. “I ended up making mounting pieces at least 3 times and had to try different gear ratios for the chain drive and even a different stepper motor with a different gear ratio. Issues were strength and flex, speed, clutch torque management and clearance under the instrument panel.”
That said, Laine is more than satisfied. “It works great,” he says. Check out a video of the RC 4210 at www.farmshow.com.
Contact: FARM SHOW Followup, Brian Laine, 7921 Wade Rd., Arlington, Wash. 98223 (ph 425 879-2890; brianlaine@aol.com; www.lainefamily.com).
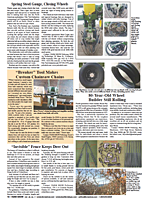
Click here to download page story appeared in.
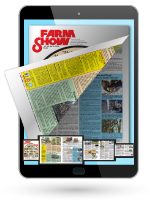
Click here to read entire issue