You have reached your limit of 3 free stories. A story preview is shown instead.
To view more stories
(If your subscription is current,
click here to Login or Register.)
How To Make Heated Water Tanks More Efficient
Heated livestock water tanks are expensive to operate and can fail in sub-zero temperatures. That’s especially true for tanks equipped with drain plug heaters and also tanks made of a single layer material, either galvanized metal or plastic, that have had heaters added onto them.
But by using recycled material
..........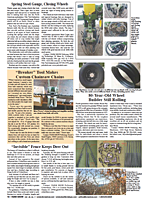
You must sign in, subscribe or renew to see the page.
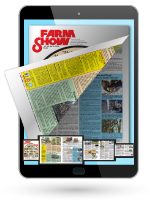
You must sign in, subscribe or renew to see the flip-book
How To Make Heated Water Tanks More Efficient LIVESTOCK Beef Heated livestock water tanks are expensive to operate and can fail in sub-zero temperatures That’s especially true for tanks equipped with drain plug heaters and also tanks made of a single layer material either galvanized metal or plastic that have had heaters added onto them But by using recycled materials it’s possible to increase a tank’s energy efficiency and also reduce freeze-up problems says Michael Thomas Salmon Idaho “If you’re filling a tank and notice the snow has melted away from it you’re wasting electricity and run the risk of sub-zero freeze-up because your heater can’t overcome the outside air temperature ” says Thomas “The idea is to create dead-air space between the tank and the outside A space of just an inch or two will dramatically reduce the energy that’s needed to keep the water from freezing ” He says 16-gal water tubs with smaller 200-watt heating elements are most susceptible to freezing at temperatures below zero “Used livestock supplement tubs work great to provide an outer jacket for these small tubs creating dead-air space around them ” says Thomas “To use this idea you’ll need a couple cans of expandable insulating spray foam per tub some waterproof filler material that can be anything from fiberglass insulation to Styrofoam packing peanuts a drill with 5/16 and 1 1/4-in drill bits and a can of all-weather spray paint ” First clean the livestock supplement tub with soap and water and let it dry Drill a 1 1/4-in dia hole on the side of the tub near the bottom for the heater’s power cord Also drill a series of 5/16-in dia holes spaced about a foot apart in the side of the tub near the bottom to allow any moisture accumulating inside to escape Then spray a layer of expandable foam onto the bottom of the tub “You don’t have to completely cover the bottom of the tub Just apply the foam in a spiral pattern from the outside toward the center ” says Thomas Allow the foam a few minutes to expand to its limit and then carefully insert the heated tub into the supplement tub drawing the heater’s power cord through the hole in the supplement tub at the same time Center the heated tub as it settles into the foam leaving a small space between the bottom of the heated tub and the supplement tub Next begin inserting filler material loosely into the space between the 2 tubs to within about 6 in of the top of the supplement tub Then apply spray foam one layer at a time Wait a few hours for the foam to cure then use a sharp knife or thin-bladed saw to trim away any excess foam Apply 2 or 3 coats of all-weather spray paint to protect the foam and then let it cure “Your newly insulated water tub is now ready to begin providing electrical savings and fewer headaches on cold winter days ” says Thomas “The same idea can be used on much larger tanks where anything from used conveyor belt material to vinyl siding can be used to create the outer jacket Any insulated space that you can create between the tank and the outside air temperature will reduce the amount of energy used and also reduce the likelihood of sub-zero tank freeze ” he notes Contact: FARM SHOW Followup Michael J Thomas 283 Withington Creek Road Salmon Idaho 83467 ph 208 756-2572; Thomasranch@centurytel net
To read the rest of this story, download this issue below or click
here to register with your account number.