2016 - Volume #40, Issue #4, Page #03
[ Sample Stories From This Issue | List of All Stories In This Issue | Print this story
| Read this issue]
They’re Turning Schoolbuses Into Greenhouses
![]() |
![]() |
![]() |
![]() |
“My family and I picked up most of the needed supplies - including the buses themselves - at local auctions over the years,” explains Doni Rae Franklin. “We converted two buses last winter.”
They started by removing all the passenger seats from the 72 and 32-passenger buses. Other than that, each modification was unique. They salvaged the drivetrain from the larger bus for another purpose, so that greenhouse is stationary, but the smaller bus is driveable, if need be.
The smaller unit has 3 poly-covered skylights installed in the roof, which let in a lot of light, but create more of an ambient, indirect lighting condition. It doesn’t get as hot inside as the larger bus, on which they replaced the entire tin roof with clear poly.
“The smaller bus’s skylights are each 3 by 3-ft, and we installed floor-level beds down both sides of the aisle. They are 16 in. deep by 3 ft. wide, by 13 ft. long,” Franklin says. “Having those beds on the floor allows us to grow taller, more productive plants. Most tomato varieties are indeterminate in height, which means they’ll actually grow to between 5 and 13 ft. tall if given the opportunity.”
Each of the three skylights were built like window frames out of 2 by 8 planks and double layers of poly, incorporating a lip to catch the roof when they were dropped into holes that they had cut. The Franklins sealed them in with silicone.
Turning the bigger bus into a greenhouse required removing the exterior and interior roof tin by cutting off the rivets. This was the hardest part of the entire project, according to family members who did the work.
Next, they took some 1 1/4-in. oilfield pipe and planed it down to create a flat side, before attaching it to the grooves of the metal roof ribs. While fitting the roof with a double layer of 6 mm poly, the Franklins took strips of soft plastic they had cut from an old walk-in-freezer curtain, and stapled them along the piped ribs, over-top of the poly. These plastic strips prevent the staples from pulling through the poly during wind storms. Inside the bus, they secured all the bottom edges of the poly with 1 by 4 boards.
They recycled the roof tin to make their planting beds, which also allowed the Franklins to avoid having any wood in direct contact with the soil. They hope that minimizes rotting problems. This was accomplished by using a plasma cutter and then folding the tin along the weakened cut lines. The beds on both buses drain onto the floor from the corners along the bottom edges.
Before installation of the planting beds, the Franklins painted the bus floors with pavement sealer to help prevent them from rusting due to humid conditions and high wear created from walking along the aisle.
“The bigger bus has raised beds that are 20 in. deep and sit 28 in. off the floor on a framework made of two by fours,” Franklin says. “This spring, we had some bad storms where we needed to use portable propane heaters inside the buses for four nights. In the fall, I plan to install permanent natural gas heaters.”
Franklin currently waters the beds with a garden hose, but is working on installing drip irrigation. She says that by only modifying the roofs and taking advantage of the buses’ existing sides and floors, she’s able to minimize heat loss from wind and ground exposure. At the same time, the multiple windows make it easy to control ventilation by opening them as needed.
Besides feeding her large household, Franklin has been building a business over the past several years by expanding her growing capacity from a simple outdoor plot, to various types of covered spaces. She produces and sells fresh produce in the summer, and also keeps busy in the winter with her specialty sales of dried vegetables and “heritage seed” from 24 varieties of tomatoes.
“As I’ve been getting more and more into commercial gardening, I’ve realized that these greenhouses are the best way to achieve a reliable harvest, stopping things like frost and hail from taking a toll,” she explains.
Since it’s mobile, the smaller bus might also be a good marketing tool in the future, Franklin says. She could garner a lot of attention if using the bus to transport fresh produce to farmer’s markets in town.
“If we ever had time to custom build one of these for someone else, we would charge about $8,000 per large bus,” Franklin says.
Contact: FARM SHOW Followup, Doni Rae Franklin, R.R. 2, Brooks, Alberta, Canada T1R 1E2 (ph 403 566-3740, cell ph 403 501-8747; donigarden@hotmail.com; https://www.facebook.com/donirae.franklin).
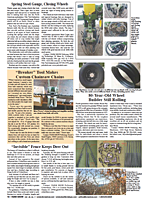
Click here to download page story appeared in.
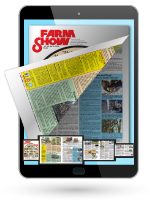
Click here to read entire issue
To read the rest of this story, download this issue below or click here to register with your account number.