2016 - Volume #40, Issue #4, Page #39
[ Sample Stories From This Issue | List of All Stories In This Issue | Print this story
| Read this issue]
He Built His Own Solar Food Dehydrator
![]() |
![]() |
![]() |
![]() |
Scheer built the solar dehydrator almost entirely from scrap aluminum that he bought at a local salvage yard. He grows apples on his 60-acre farm and expects to use the dehydrator in a big way this fall.
The dehydrator measures 12 ft. long by 4 ft. wide and is built in 3 sections. Each section has a pair of hinged doors for access.
“It’s big, and when the sun is out the aluminum makes it gleam like a jet,” says Scheer. “I built it because I wanted a more energy efficient dehydrator that can turn large quantities of apples into chips that we can sell. Solar dehydrators let you dry food for free year after year, which appeals to me. I looked at all the other solar dehydrator designs and decided this one is the simplest and most failsafe.
“It’s based on a design created by Larisa Walk and Bob Dahse of Winona, Minn. They built their first solar dehydrator in the 1980’s, and now there are hundreds of them in the U.S. and abroad. It’s designed to be built by small farmers but can easily be scaled up for commercial production. The key to its success is its simplicity - avoiding complex energy conversions and reducing heat movement as much as possible.”
But Scheer took the Walk dehydrator design one step farther by making his dehydrator entirely out of aluminum. “Aluminum is easier to clean than plywood and should hold up better over time, without cracking, chipping or rotting,” says Scheer. “Another advantage of using aluminum is that scrap aluminum is cheap and readily available. My dehydrator’s foundation is made from 12-ft. aluminum I-beams that weigh 3 to 4 lbs. apiece. With scrap aluminum selling for about $1 to $2 per pound, I was able to build my dehydrator for less than $100.”
He started building the dehydrator two years ago. “A small farmer in northern Minnesota proposed a dehydrator experiment to a University of Minnesota extension service funding agency and enrolled me in it. We’re comparing my dehydrator with two other designs in three different locations, and so far mine compares favorably. The university would like to see the results made public so that others can benefit.”
Here’s the design, from top to bottom.
Sunlight shines through clear twin-wall polycarbonate glazing (typically found in greenhouses) which protects the collector from the elements and helps create an insulating air space. The sunlight heats up black-painted aluminum sheet metal, and the back side of the black aluminum re-radiates infrared heat into the food below it, which sets on stainless steel screens. Moisture given off by the drying food passively flows out under the screens and up sloped air channels underneath the screens.
Building plans for the Walk solar dehydrator are available at www.geopathfinder.com/solar-food-drying.html.
Contact: FARM SHOW Followup, Kent Scheer, 850 Scheer Drive N.E., Wadena, Minn. 56482 (ph 218 631-3084; kentscheer@outlook.com).
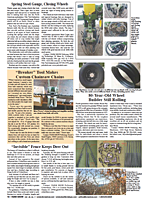
Click here to download page story appeared in.
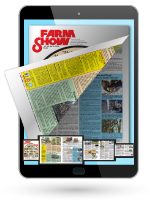
Click here to read entire issue
To read the rest of this story, download this issue below or click here to register with your account number.