Air System Designed To Improve Combine Rotor Performance
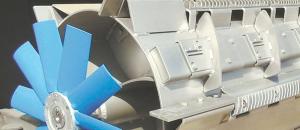 ✖  |
Specialty combine parts manufacturer Sunnybrook Welding in Alberta, Canada is testing a new axial fan system to improve crop separation in rotary combines. Gerald Foster of Sunnybrook says their Axial Air Integrated Rotor (AAIR) uses air pressure to separate grain from residue, or seed from straw.
The AAIR system pressurizes the inside of the rotor with a 10-blade fan, which forces air into a 3-blade centrifugal fan inside the rotor. As the rotor turns, a steady stream of air moves into the rotor and out the sides, through adjustable louvers. Adjustable slides allow the operator to fine tune the setting to gain maximum threshability.
Foster says Sunnybrook is running tests in 2016 with a Gleaner S Series machine. The company manufactured aftermarket rotors for those combines from 2002 to 2012, so they’re very familiar with them. The test rotor is being modified so it’s 75 percent open to let air move from the front axial to the centrifugal fan. The machine operator changes air flow by adjusting a steel disc covering the opening.
Another modification includes cutting the end wall spool from the rotor and moving it 10 in. in from its original position. This space allows mounting the blue blade axial fan and 3 curved steel fan vanes inside the rotor wall. Foster says they’re using high quality axial fans and mounting them on a shaft that accelerates from 0 to 1,000 rpm in just two revolutions of the shaft.
Air is funneled out of the rotor by the 3 curved centrifugal blades through hollow steel channels welded to the outside of the rotor. The channels run the full length of the rotor and are capped to hold air pressure. Each channel has 6 louvers 3 in. long and 1/2 in. wide that release air through the crop mat. Each channel is adjustable to regulate air flow.
Foster says company engineers think the increased air flow can benefit a machine’s output because material will flow through more evenly and grain will separate more uniformly from the residue across the full diameter and length of the rotor. Long term Foster says the goal is to reduce friction in the threshing chamber, conserve power and put more material through the machine.
Contact: FARM SHOW Followup, Sunnybrook Welding & Machine Shop Ltd., P.O. Box 28, Sunnybrook, Alberta Canada T0C 2M0 (ph 780 789-3855; www.sunnybrookwelding.com).
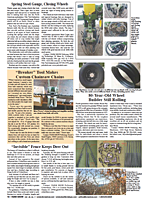
Click here to download page story appeared in.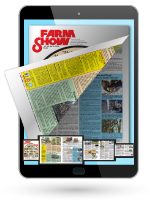
Click here to read entire issue
Air System Designed To Improve Combine Rotor Performance COMBINES Accessories Specialty combine parts manufacturer Sunnybrook Welding in Alberta Canada is testing a new axial fan system to improve crop separation in rotary combines Gerald Foster of Sunnybrook says their Axial Air Integrated Rotor AAIR uses air pressure to separate grain from residue or seed from straw The AAIR system pressurizes the inside of the rotor with a 10-blade fan which forces air into a 3-blade centrifugal fan inside the rotor As the rotor turns a steady stream of air moves into the rotor and out the sides through adjustable louvers Adjustable slides allow the operator to fine tune the setting to gain maximum threshability Foster says Sunnybrook is running tests in 2016 with a Gleaner S Series machine The company manufactured aftermarket rotors for those combines from 2002 to 2012 so they’re very familiar with them The test rotor is being modified so it’s 75 percent open to let air move from the front axial to the centrifugal fan The machine operator changes air flow by adjusting a steel disc covering the opening Another modification includes cutting the end wall spool from the rotor and moving it 10 in in from its original position This space allows mounting the blue blade axial fan and 3 curved steel fan vanes inside the rotor wall Foster says they’re using high quality axial fans and mounting them on a shaft that accelerates from 0 to 1 000 rpm in just two revolutions of the shaft Air is funneled out of the rotor by the 3 curved centrifugal blades through hollow steel channels welded to the outside of the rotor The channels run the full length of the rotor and are capped to hold air pressure Each channel has 6 louvers 3 in long and 1/2 in wide that release air through the crop mat Each channel is adjustable to regulate air flow Foster says company engineers think the increased air flow can benefit a machine’s output because material will flow through more evenly and grain will separate more uniformly from the residue across the full diameter and length of the rotor Long term Foster says the goal is to reduce friction in the threshing chamber conserve power and put more material through the machine Contact: FARM SHOW Followup Sunnybrook Welding & Machine Shop Ltd P O Box 28 Sunnybrook Alberta Canada T0C 2M0 ph 780 789-3855; www sunnybrookwelding com
To read the rest of this story, download this issue below or click
here to register with your account number.