He Built His Own Milk “Precooler”
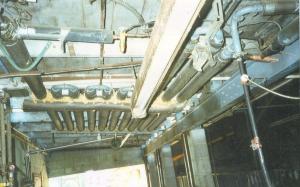 ✖  |
When one of two bottom cooling units in James Martin’s 3,500-gal. milk cooler failed, he bought a commercial precooler, but it couldn’t keep up to the milk flow. Fixing the cooler would have required extensive repairs. That wasn’t possible when cows are being milked twice a day. So Martin designed and fabricated a unit to chill milk to 47 degrees before it entered the big cooler.
“I couldn’t get refrigeration guys to build a precooler for me, so I did it myself,” says Martin. “I used 1 5/8-in. stainless steel tubing inside 2-in. copper and introduced compressed Freon between the 2 tubes.
“I figure I used 127 ft. of stainless steel,” says Martin. “I invested about $3,000 in it, which was worth it because it kept my milk qualifying for the Grade A premium.”
Martin set the system up so the compressor would kick in after the milk pump did. Martin had to experiment with expansion valves for the Freon to get the right cooling rate. If the milk got too cold, it would freeze. He put a thermosensor in the exiting milk to shut down the compressor if the temperature dropped too much. Otherwise, it shut down when the milk pump stopped.
“I used it for about 10 years before I quit dairying,” says Martin. “It only froze up about 10 times in all those years. We milked for about 15 hours a day in 2 shifts and could put milk in the tank at 47 degrees in the summer.”
Cleaning the system was easy, he adds. When the milk shift ended, about 10 gal. of milk would remain in the precooler. It would be drained and fed to dairy calves. The same wash cycle that cleaned the dairy’s pipeline milking system cleaned the precooler.
“I was careful to use components from a dairy supply store,” says Martin. “I talked to my federal dairy inspector first and never cut any corners.”
Contact: FARM SHOW Followup, James Martin, 13580 E. Sargent Rd., Lodi, Calif. 95240 (ph 209 333-2359).
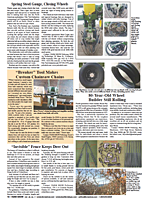
Click here to download page story appeared in.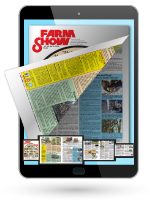
Click here to read entire issue
He Built His Own Milk “Precooler” DAIRY EQUIPMENT & IDEAS When one of two bottom cooling units in James Martin’s 3 500-gal milk cooler failed he bought a commercial precooler but it couldn’t keep up to the milk flow Fixing the cooler would have required extensive repairs That wasn’t possible when cows are being milked twice a day So Martin designed and fabricated a unit to chill milk to 47 degrees before it entered the big cooler “I couldn’t get refrigeration guys to build a precooler for me so I did it myself ” says Martin “I used 1 5/8-in stainless steel tubing inside 2-in copper and introduced compressed Freon between the 2 tubes “I figure I used 127 ft of stainless steel ” says Martin “I invested about $3 000 in it which was worth it because it kept my milk qualifying for the Grade A premium ” Martin set the system up so the compressor would kick in after the milk pump did Martin had to experiment with expansion valves for the Freon to get the right cooling rate If the milk got too cold it would freeze He put a thermosensor in the exiting milk to shut down the compressor if the temperature dropped too much Otherwise it shut down when the milk pump stopped “I used it for about 10 years before I quit dairying ” says Martin “It only froze up about 10 times in all those years We milked for about 15 hours a day in 2 shifts and could put milk in the tank at 47 degrees in the summer ” Cleaning the system was easy he adds When the milk shift ended about 10 gal of milk would remain in the precooler It would be drained and fed to dairy calves The same wash cycle that cleaned the dairy’s pipeline milking system cleaned the precooler “I was careful to use components from a dairy supply store ” says Martin “I talked to my federal dairy inspector first and never cut any corners ” Contact: FARM SHOW Followup James Martin 13580 E Sargent Rd Lodi Calif 95240 ph 209 333-2359
To read the rest of this story, download this issue below or click
here to register with your account number.