1988 - Volume #12, Issue #3, Page #02
[ Sample Stories From This Issue | List of All Stories In This Issue | Print this story
| Read this issue]
Build Yourself A Bridge
If you're in need of a low cost bridge to get machinery or people across a river or wide creek, this home made "Bridge Over The River Zumbro" might be just the ticket.It was designed and built as a family project by John and Dorothy Zemke and their children David, Joy and Daniel. The Zemkes own land on both sides of the Zumbro river near Pine Island in southeast-ern Minnesota. Getting from one side to the other the long way around meant traveling 1.5 miles. Their suspension bridge shortened that distance to 123 ft.
The Zemkes plan to develop a camp-ground on their wooded land located across the river from their farm headquarters. Their primary purpose in building the bridge was to create a handy passageway for persons to walk back and forth, and for light equipment, such as ATV's, snowmobiles and garden tractors. "The bridge is 6 ft. wide and will easily support ten people weighing 200 lbs. each," says John who regularly crosses it with a "3 wheeler" and trailer loaded with upwards of 800 lbs. of chainsaws and other equipment. "By beefing up the wood floor and making it wider, you could easily adapt this basic design to build yourself a suspension bridge wide enough and strong enough to support machinery, cars, trucks, and other equipment."
The bridge-building project began in the spring of '87 with family members and friends supplying technical know-how and labor.
David, an engineering student, assisted in designing the bridge and drawing blue-prints. The final draft was sent to the Department of Natural Resources (DNR) and, over a period of several months, made its way to the U.S. Army Corp of Engineers. Because 100 ft. on each side of the river is controlled by the DNR, final approval rested in their hands.
"We had to sign an affidavit holding us responsible for any damage done in the event the bridge would happen to turn into a dam and cause damage upstream," John told FARM SHOW. "We don't anticipate any problems. In an unusually high water emergency, it would only take us about 15 minutes lead time to loosen support cables so the wooden walkway would hang vertically and swing if hit by floating logs, ice chunks or whatever. If the high water hit before we could loosen cables, the bridge would still be high enough to withstand an unusually severe flood emergency."
The two giant pillars supporting the bridge are 123 ft. apart and stand 22 ft. above ground level. They're made in three sections. The bottom section, which ex-tends about 5 ft. underground, is made of concrete culvert measuring 21 in. inside dia. Setting on top of it is a smaller concrete culvert measuring 12 in. inside dia. The top section is a 9 in. dia PVC pipe which ex-tends down into the middle section. Vertical reinforcing rods and concrete, poured inside the culverts and around the rods, and inside the PVC pipe, strengthen each pillar. They're set on concrete footings measuring 8 ft. by 12 ft. by 1 ft. thick,
The two horizontal cables spanning the bridge are 7/8 in. in dia. and are anchored at each end by 10 ft. support posts made of 21 in. dia. concrete culverts buried 5 ft. in the ground and filled with concrete and rebar. The anchors are connected to concrete footings measuring 6 ft. by 12 ft. by 1 ft. thick. Vertical support cables are 3/8 in. in dia. and spaced 6 ft. apart.
To allow for seasonal contraction and expansion, the Zemkes installed car springs in the middle of the bridge. Treated planking for the floor (1-1/4 by 6 in. by 6 ft. long) carries a 40 year "no maintenance needed" warranty.
The final step to be completed this spring is to add side rails, made of 42 in. high chain link fence. It'll be supported horizontally along the top with a piece of 3/8 in. dia. cable, and secured to existing 3/8 in. vertical support cables.
John says his total out-of-pocket cost for materials was under $3,000. The "bargain price" concrete culverts were seconds and the 7/8 in. cable, salvaged from a crane, was purchased "dirt cheap." The single most expensive item was the treated, round cornered (to reduce slivering) patio lumber used to make the walkwa
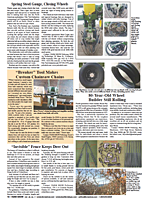
Click here to download page story appeared in.
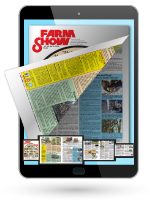
Click here to read entire issue
To read the rest of this story, download this issue below or click here to register with your account number.