You have reached your limit of 3 free stories. A story preview is shown instead.
To view more stories
(If your subscription is current,
click here to Login or Register.)
Loader Bucket-Sized Compost Sifter
After years of screening compost into a wheelbarrow, Rod Stremlo’s big sifter handles compost by the loader bucket. It turns a laborious and time-eating chore into a quick and speedy task at the family’s Brook Hollow Farm.
“It took me 45 min. to sift out a wheelbarrow full of compost and a lot of shoveling,”
..........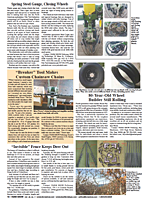
You must sign in, subscribe or renew to see the page.
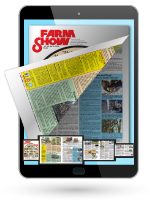
You must sign in, subscribe or renew to see the flip-book
Loader Bucket-Sized Compost Sifter TRACTORS Loaders After years of screening compost into a wheelbarrow Rod Stremlo’s big sifter handles compost by the loader bucket It turns a laborious and time-eating chore into a quick and speedy task at the family’s Brook Hollow Farm “It took me 45 min to sift out a wheelbarrow full of compost and a lot of shoveling ” says Stremlo “We need 2 or 3 tons of compost to build new garden beds Now I do a loader bucket full in a few minutes ” Stremlo’s sifter is 2 ft wide and 12 ft long It’s mounted on a frame made from old goal posts and steel tubing Uprights at the upper end where the engine sits were salvaged from an old mobile home trailer tongue The sifter was designed to leave room underneath it for the loader to retrieve a bucketful The lower end of the screen leaves room for a wheelbarrow to be pushed underneath it to collect larger particles and materials not fully composted They are wheeled back to the composting pile “I’ve found the returns speed up the composting process ” says Stremlo Most of the sifter was recycled from one use or another but the motor with factory installed gear reducer was actually fresh out of the box Stremlo purchased it at a yard sale He later found out that it sat on a shelf for 20 years “I put gas and oil in it and it started right up ” he says The screen is slotted expanded mesh with an overlay of “rat wire” hardware cloth Stremlo added the hardware cloth to reduce the hole size and resulting particle size The screen frame rides on plastic wheels that are mounted to uprights on the main frame The sifting screen moves up and down at an angle with finished compost sifting through and large scraps needing more time in the compost pile falling off the end The sifter is powered by a 3 1/2 hp motor with a built-in 6-to-1 gear reducer The output shaft with a small sheave drives a larger old cast iron sheave on an old air compressor pump This reduces the output shaft speed even more As the air compressor pump’s only purpose is to provide a housing for the drive sheave Stremlo removed the pistons and rod and filled the compressor with oil He drilled a 3/8-in hole in the arms of the cast iron sheave 3/4-in from the center of the shaft and installed a grade-8 bolt in the hole Once the offset bolt was connected to the screen it provided about 1 1/2 in of lateral movement with every revolution The connecting arm is a set of shock absorber type springs from an old conveyer dishwasher “One spring in the pair regulates how hard it pushes the screen downhill and the other regulates how hard it pulls the screen back up the slope ” says Stremlo “When the screen slides downhill the engine has to work hard pulling it back up The spring reduces that effort ” Stremlo notes that his sifter isn’t quite finished If he dumps raw compost onto the screen too fast it can stop the screen in its tracks “The answer may be to mount a hopper from a pickup-mounted salt spreader ” says Stremlo “It would better regulate how fast compost drops onto the screen ” Meanwhile Stremlo remains satisfied with his design and its price tag “I only have about $200 in it and half of that was for the paint I used ” says Stremlo “I did a good job painting it when it was new ” Check out a video of Stremlo’s compost sifter at FARMSHOW com Contact: FARM SHOW Followup Brook Hollow Farm ph 732 947-2778; jstremlo@gmail com
To read the rest of this story, download this issue below or click
here to register with your account number.