You have reached your limit of 3 free stories. A story preview is shown instead.
To view more stories
(If your subscription is current,
click here to Login or Register.)
Giant Wash Rig Cleans Big Sprayers
Neil Welsh keeps his spray rig and himself clean with his drive-thru equipment washer. The 17-ft. tall legs and 20-ft. crossbeam with integrated booms and nozzles make it easy to keep the 1,500-gal. Miller Nitro sprayer clean. The 20-year old does most of the spraying for his family’s farming operation. He is also resp
..........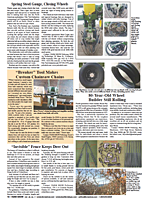
You must sign in, subscribe or renew to see the page.
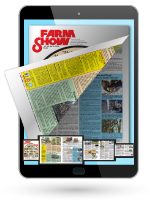
You must sign in, subscribe or renew to see the flip-book
Giant Wash Rig Cleans Big Sprayers CLEANING EQUIPMENT Neil Welsh keeps his spray rig and himself clean with his drive-thru equipment washer The 17-ft tall legs and 20-ft crossbeam with integrated booms and nozzles make it easy to keep the 1 500-gal Miller Nitro sprayer clean The 20-year old does most of the spraying for his family’s farming operation He is also responsible for keeping the tall sprayer clean “With a front boom you are driving into the spray mist all day long ” says Welsh “The sprayer gets coated with chemicals and road dust After a couple of days spraying even a new sprayer starts to show signs of corrosion It’s hard to spray it off with a hand wand without getting the chemicals and dirt on your body and clothes ” Welsh designed the washing unit to clean away the bulk of the day’s deposits The triangular structure consists of three 2-in schedule 80 stainless steel pipes locked at 2-ft distances in a cross web of 1 3/4-in dia 1/4-in thick steel pipes The pipe structure is strong enough to serve as its own ladder for maintenance The 2 pipes forming the base of the triangular structure are plumbed to deliver 180 gal of water at 150 lbs pressure The water blasts equipment passing through from flat fan nozzles positioned at opposing 35-degree angles and staggered every foot Separate spray nozzles mounted at ground level direct water up and into the inside wheel wells “The angle of the nozzles ensures that the sprayer gets hit by streams of water from 2 directions not just straight on ” says Welsh who built the washer as a 4-H project “The Hypro 4200 pump is unusual with its impeller shape It’s hard to get both volume and pressure but this one offers both ” Welsh built the entire system from stainless steel so it would stand up to the corrosive chemicals An accomplished metal worker cutting and drilling the stainless steel was less of a challenge than getting the web of pipes bolted to each other “I used an auto-feed drill press to drill the sixty plus holes that were needed ” says Welsh “The flanges had to be perfectly square so the bolt holes all lined up ” Although the spray season is limited the structure is left up year round Drain valves at the bottom of water carrying pipes empty them at season’s end The entire pump system is enclosed to the side of the structure for easy disconnecting and moving to storage with a forklift Currently the washer framework is bolted to large concrete slabs at either side Plans are to install a concrete pad that will be used both for washing sprayers and filling A drain will direct wastewater to an evaporation ponding area At that point other changes may be made such as placing undercarriage tips in the pad and using a larger pump or multiple pumps one on either side for higher pressure Welsh notes that the third pipe could also be used to carry water “We may add a cleaning solution tank for use every few days ” says Welsh “We will be installing reverse osmosis water treatment to make the washer work better but also to improve the spray solution quality ” Check out a video of Welsh’s washer at www farmshow com Contact: FARM SHOW Followup Neil Welsh 2228 Y Ave Williamsburg Iowa 52361 ph 319 530-5431; neilwelsh95@gmail com
To read the rest of this story, download this issue below or click
here to register with your account number.