“Built-From-Scratch” High-Horsepower Power Unit
Eddie Eron was looking for a way to power a silo blower and silo bagger, as well as a 220-hp. rated liquid manure pump, without tying up an expensive big tractor. He ended up building a 2-WD self-propelled power unit from a junked-out semi-truck and other parts. It’s powered by a 335-hp. diesel engine from the semi-truck and equipped with a 1,000 rpm pto. It rides on big combine tires on the back and semi-truck tires on the front, and you can’t miss the 275-gal. fuel tank located above the front wheels.
The power unit’s engine, transmission, and transfer case are mounted backward so the pto shaft will rotate in the opposite direction as the engine. The driver sits on the right side of the machine.
“I call it the Grunt because it does a lot of heavy work,” says Eron, who built the unit 2 years ago. “It took me about 2 mos. working in my spare time to build it, and I engineered most of it on the fly. It does nearly everything a traditional high-horsepower tractor can do. But it’s not really a tractor because it can’t pull an implement and pto-drive at the same time. I spent less than $5,000 to build it.
“Originally, I thought about repowering one of my existing tractors with a bigger engine, but I was worried the extra power might cause problems. By building from scratch, I was able to use heavy-duty components that I know will hold up. Also, everything is out in the open, so I can remove any of the major components without having to remove something else.”
Eron is a part-time mechanic who operates his own shop and also works at a local farm, where he does most of the maintenance work. He got the idea for the power unit while working for a local farmer who had a 12-ft. silo bagger that required a 220-hp. tractor. The farmer didn’t have a tractor that big.
“All the feed that goes to the farmer’s 175 milking cows, including haylage, corn silage, and high-moisture corn, goes through my power unit,” says Eron. “For example, he can use the power unit to pull the bag loader to the bag and then pto-drive it. As the bag fills, the bag loader pushes the power unit along just like with a tractor.
“I’ve heard of other farmers who made a power unit by mounting a truck engine and a gearbox or combine final drive on a wagon running gear in order to reduce the rpm’s and reverse the rotation of the pto shaft. However, you need a tractor to tow those units into place.”
Eron got the Cummins diesel engine from a 1978 Ford Louisville semi-truck that had been sitting in the woods since 1991. He also salvaged the truck’s 9-speed transmission, frame, front differential, steering axle and wheels, steering box, air brakes, bumper, muffler, air cleaner, and seat. The transfer case is off a 5-ton military truck. The rear axle is off the semi-truck and fitted with the front tires off an old Deere combine.
He welded two semi-truck frames together, one on top of the other. “The stacked frames raise the engine high enough to clear the pto driveline,” he says.
He says the most difficult part of the job was figuring out how to modify the power divider on the semi-truck’s front drive axle so the pto can be turned on or off.
“Most semi-trucks have two drive axles, and the drive shaft extends from the power divider on the front axle back to the rear axle,” says Eron. “Normally, the power divider directs half its power to the front drive axle and half to the rear axle. However, I wanted all the power going out the rear of the axle, so I welded the power divider solid. I also removed one of the gears in the power divider so that it won’t turn the tires unless it’s locked.”
An air switch off the semi-truck is used to switch from driving mode to pto mode. “Flipping the switch one way locks the power divider so I can drive the unit. Flipping the switch the other way unlocks the power divider so that it drives just the pto shaft without turning the rear wheels. Then both the power unit and bagger will just freewheel as the bag is filled with grain or silage,” says Eron.
“I put the 9-speed transmission in 9th gear to operate the pto at 1,000 rpm’s and in 6th gear to operate at 540 rpm’s. Our silo bagger and manure pump both operate at 1,000 rpm’s. However, our Case IH 600 silo blower has a 540 pto so I installed a 1,000 rpm yoke on the silo blower so it will fit the Grunt’s pto shaft.”
To install the combine tires on the semi-truck axle, Eron cut the centers out of the wheel rims. Then he welded in a pair of 10-bolt truck wheel centers and bolted the tires on.
The machine has side-by-side brake pedals, one for each rear wheel. “The brake pedals came off two different trucks that had the same pedal and brake valve assemblies,” says Eron.
He paid $400 for the truck and spent about $1,000 to rebuild the engine’s fuel injectors and pump. He paid $300 for the transfer case.
Contact: FARM SHOW Followup, Eddie Eron, N12383 Hixton Levis Road, Fairchild, Wis. 54741 (ph 715-533-4701; esemachine@centurylink.net).
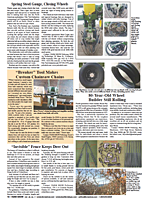
Click here to download page story appeared in.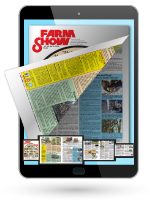
Click here to read entire issue
“Built From Scratch” High Horsepower Power Unit TRACTORS Made-It-Myself Eddie Eron was looking for a way to power a silo blower and silo bagger as well as a 220 hp rated liquid manure pump without tying up an expensive big tractor He ended up building a 2-WD self-propelled power unit from a junked-out semi truck and other parts It’s powered by a 335 hp diesel engine from the semi truck and equipped with a 1 000 rpm pto It rides on big combine tires on back and semi truck tires on front and you can’t miss the 275-gal fuel tank located above the front wheels The power unit’s engine transmission and transfer case are mounted backward so the pto shaft will rotate in the opposite direction as the engine The driver sits on the right side of the machine “I call it the Grunt because it does a lot of heavy work ” says Eron who built the unit 2 years ago “It took me about two months working in my spare time to build it and I engineered most of it on the fly It does nearly everything a traditional high horsepower tractor can do But it’s not really a tractor because it can’t pull an implement and pto-drive at the same time I spent less than $5 000 to build it “Originally I thought about repowering one of my existing tractors with a bigger engine but I was worried the extra power might cause problems By building from scratch I was able to use heavy-duty components that I know will hold up Also everything is out in the open so I can remove any of the major components without having to remove something else ” Eron is a part-time mechanic who operates his own shop and also works at a local farm where he does most of the maintenance work He got the idea for the power unit while working for a local farmer who had a 12-ft silo bagger that required a 220 hp tractor The farmer didn’t have a tractor that big “All the feed that goes to the farmer’s 175 milking cows including haylage corn silage and high moisture corn goes through my power unit ” says Eron “For example he can use the power unit to pull the bag loader to the bag and then pto-drive it As the bag fills the bag loader pushes the power unit along just like with a tractor “I’ve heard of other farmers who made a power unit by mounting a truck engine and a gearbox or combine final drive on a wagon running gear in order to reduce the rpm’s and reverse the rotation of the pto shaft However you need a tractor to tow those units into place ” Eron got the Cummins diesel engine from a 1978 Ford Louisville semi truck that had been sitting in the woods since 1991 He also salvaged the truck’s 9-speed transmission frame front differential steering axle and wheels steering box air brakes bumper muffler air cleaner and seat The transfer case is off a 5-ton military truck The rear axle is off the semi truck and fitted with the front tires off an old Deere combine He welded two semi truck frames together one on top of the other “The stacked frames raise the engine high enough to clear the pto driveline ” he says He says the most difficult part of the job was figuring out how to modify the power divider on the semi truck’s front drive axle so the pto can be turned on or off “Most semi trucks have two drive axles and the drive shaft extends from the power divider on the front axle back to the rear axle ” says Eron “Normally the power divider directs half its power to the front drive axle and half to the rear axle However I wanted all the power going out the rear of the axle so I welded the power divider solid I also removed one of the gears in the power divider so that it won’t turn the tires unless it’s locked ” An air switch off the semi truck is used to switch from driving mode to pto mode “Flipping the switch one way locks the power divider so I can drive the unit Flipping the switch the other way unlocks the power divider so that it drives just the pto shaft without turning the rear wheels Then both the power unit and bagger will just freewheel as the bag is filled with grain or silage ” says Eron “I put the 9-speed transmission in 9th gear to operate the pto at 1 000 rpm’s and in 6th gear to operate at 540 rpm’s Our silo bagger and manure pump both operate at 1 000 rpm’s However our Case IH 600 silo blower has a 540 pto so I installed a 1 000 rpm yoke on the silo blower so it will fit the Grunt’s pto shaft ” To install the combine tires on the semi truck axle Eron cut the centers out of the wheel rims Then he welded in a pair of 10-bolt truck wheel centers and bolted the tires on The machine has side-by-side brake pedals one for each rear wheel “The brake pedals came off 2 different trucks that had the same pedal and brake valve assemblies ” says Eron He paid $400 for the truck and spent about $1 000 to rebuild the engine’s fuel injectors and pump He paid $300 for the transfer case Contact: FARM SHOW Followup Eddie Eron N12383 Hixton Levis Road Fairchild Wis 54741 ph 715 533-4701; esemachine@centurylink net
To read the rest of this story, download this issue below or click
here to register with your account number.