You have reached your limit of 3 free stories. A story preview is shown instead.
To view more stories
(If your subscription is current,
click here to Login or Register.)
Rotating Culvert Turns Waste Into Compost
Ron Harwood’s 2-ft. dia., tubular composter is a culvert on wheels. Set at an angle that falls 2 ft. over its 20-ft. length, daily turning aerates the compostable materials and moves them slowly toward their finished state.
“The incline moves the organic material being composted and also encourages convectio
..........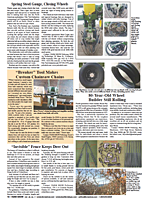
You must sign in, subscribe or renew to see the page.
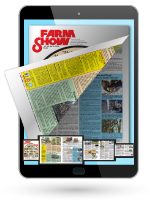
You must sign in, subscribe or renew to see the flip-book
Rotating Culvert Turns Waste Into Compost CROPS Miscellaneous Ron Harwood’s 2-ft dia tubular composter is a culvert on wheels Set at an angle that falls 2 ft over its 20-ft length daily turning aerates the compostable materials and moves them slowly toward their finished state “The incline moves the organic material being composted and also encourages convection of the air to keep the material oxygenated ” explains Harwood “If it is too steep the material moves too fast to fully compost ” Harwood and his wife Melissa operate a small Maine farm where they raise a few animals some crops including hay and a large unique container garden The containers are 5-gal buckets filled with a mix of compost and soil Legally blind since 2012 Harwood finds it easier to garden with the buckets than with conventional garden beds However they require a lot of compost and the tubular composter provides it The Harwoods make compost from the time they first mow their lawn in the spring until December Each day they dump about three 5-gal buckets of kitchen and garden scraps and animal manure into the upper end of the composter About 5 to 6 weeks later the compost is ready The initial compostable materials fill nearly two-thirds the diameter of the first foot of the culvert This thins out to half the diameter as it moves down the length of the tube The reduced depth makes it harder to maintain biological activity An engineer by training Harwood has ideas to improve his design He plans to add 5 internal rings with variable pitch paddles inside the cylinder to slow movement of the material downhill “Our goal is 3 weeks for finished compost ” says Harwood “We hope that adding the paddles will restrict the flow of the material and keep it thicker for better biological activity ” The tubular composter rests on seven 2 by 6-in crosspieces each with 2 caster wheels that fit into the culvert’s grooves The 2 by 6’s ride on two 16-ft long 6 by 6-in hemlock timbers They in turn rest on 2 shorter hemlock timbers at each end of the composter Vented caps with variable dampers at either end can be adjusted to control air and temperature Four holes cut into the lower end of the culvert let Harwood turn it by hand “I estimate it holds about 1 200 lbs but with the leverage of a 4-ft pipe it is easy to turn ” says Harwood Even without the paddles the composter does the job Harwood reports only a couple of failures when the outside temperature was more than 90 degrees for several days The internal temperature got too hot and pasteurized the material The Harwoods have learned not to put hay or other long-fiber material into the composter “It comes out like a rope at the other end ” says Harwood As the material exits the composter Harwood collects it in a tote bag that he can move with forks on his tractor “I spent my career problem solving as part of a team ” says Harwood “We would love to hear how others might make use of this idea ” Contact: FARM SHOW Followup Ron and Melissa Harwood P O Box 10 Harmony Maine 04942 ph 207 717-7898; RonAndLissaHarwood@outlook com
To read the rest of this story, download this issue below or click
here to register with your account number.