Shop-Built Boring Tool
Maryland handyman Brian Lough built his own line-boring machine because he couldn’t justify the cost of a commercial model. He needed it to enlarge the bore of the pin holes on his 12-in. used excavator bucket. “I knew I could make something fairly simple that would work just fine using a drill, a scissor jack, and other parts in my shop,” says Lough.
The other parts include C-channel, 1 1/2-in. bearings, bearing mounting blocks, a bit setting tool, pvc centering cones, a 1 1/2-in. shaft coupler with key stock, and a short shaft turned down for a 1/2-in. drill motor. He fabricated the boring bar from a 1 1/2-in. keyed shaft with 1/2-in. square holes spaced 5-in. apart. Set screws are rotated 90-degrees from the square hole to lock the boring bit.
Lough secured the bearings with pieces of 1-in. square bar 4 1/2-in. long, threaded on the bearing end and welded to the part on the opposite end. He welded one edge of the bar so when boring was complete he could tap on the opposite side of the weld to break it loose. Then he ground the weld flush so he could re-use the bar. Lough says small metal plates could be welded to a part to extend the reach of the mounting bar.
“I fabricated a bit-setting tool that uses a feller gauge to determine the advance needed for the next cut,” Lough says. His lathe tool was made from 1/2-in. square HSS stock shaped with a round nose so it would cut in both directions. The cutting edge height was reduced 1/4-in. so it cuts to the centerline axis of the bore.
Lough’s machine can also be used for repairing out-of-round holes. In that application he installs a sleeve with the correct inside diameter, or welds the inside of the bore, then cuts it to the correct diameter. Lough says anyone welding before boring needs to make sure all grease is removed or that area will harden and not cut correctly.
“This setup worked great for what I needed, and although I don’t have any formal drawings on building another one, I’ll be happy to help anyone who wants to build their own. It took me about 30 hrs. to put the tool together and I spent about $125 for the bearings, shaft, shaft coupler and screw jack. A commercial tool would’ve cost about $2,000,” Lough adds.
Contact: FARM SHOW Followup, Brian Lough, 5860 Smallwood Church Road, Indian Head, Md. 20640 (ph 301 246-9092; brianlough@hughes.net).
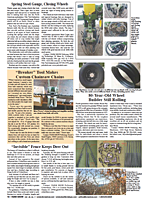
Click here to download page story appeared in.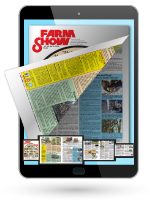
Click here to read entire issue
Shop-Built Boring Tool FARM SHOP Miscellaneous Maryland handyman Brian Lough built his own line-boring machine because he couldn’t justify the cost of a commercial model He needed it to enlarge the bore of the pin holes on his 12-in used excavator bucket “I knew I could make something fairly simple that would work just fine using a drill a scissor jack and other parts in my shop ” says Lough
The other parts include C-channel 1 1/2-in bearings bearing mounting blocks a bit setting tool pvc centering cones a 1 1/2-in shaft coupler with key stock and a short shaft turned down for a 1/2-in drill motor He fabricated the boring bar from a 1 1/2-in keyed shaft with 1/2-in square holes spaced 5-in apart Set screws are rotated 90-degrees from the square hole to lock the boring bit
Lough secured the bearings with pieces of 1-in square bar 4 1/2-in long threaded on the bearing end and welded to the part on the opposite end He welded one edge of the bar so when boring was complete he could tap on the opposite side of the weld to break it loose Then he ground the weld flush so he could re-use the bar Lough says small metal plates could be welded to a part to extend the reach of the mounting bar
“I fabricated a bit-setting tool that uses a feller gauge to determine the advance needed for the next cut ” Lough says His lathe tool was made from 1/2-in square HSS stock shaped with a round nose so it would cut in both directions The cutting edge height was reduced 1/4-in so it cuts to the centerline axis of the bore
Lough’s machine can also be used for repairing out-of-round holes In that application he installs a sleeve with the correct inside diameter or welds the inside of the bore then cuts it to the correct diameter Lough says anyone welding before boring needs to make sure all grease is removed or that area will harden and not cut correctly
“This setup worked great for what I needed and although I don’t have any formal drawings on building another one I’ll be happy to help anyone who wants to build their own It took me about 30 hrs to put the tool together and I spent about $125 for the bearings shaft shaft coupler and screw jack A commercial tool would’ve cost about $2 000 ” Lough adds
Contact: FARM SHOW Followup Brian Lough 5860 Smallwood Church Road Indian Head Md 20640 ph 301 246-9092; brianlough@hughes net
To read the rest of this story, download this issue below or click
here to register with your account number.