You have reached your limit of 3 free stories. A story preview is shown instead.
To view more stories
(If your subscription is current,
click here to Login or Register.)
Continuous-Flow “Biochar” Reactor Built From Scrap
Bruce Saunders turns wood chips and sawdust into biochar with his homemade, continuous flow biochar machine. For anyone who’s not familiar with it, biochar is basically charcoal, made from organic material, that’s used as a soil amendment and feed additive.
He used scrap pipe, an old feed mixer, and an
..........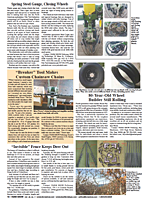
You must sign in, subscribe or renew to see the page.
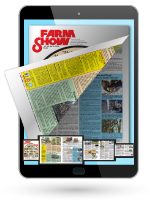
You must sign in, subscribe or renew to see the flip-book
Continuous-Flow “Biochar” Reactor Built From Scrap CROPS Miscellaneous Bruce Saunders turns wood chips and sawdust into biochar with his homemade continuous flow biochar machine For anyone who’s not familiar with it biochar is basically charcoal made from organic material that’s used as a soil amendment and feed additive
He used scrap pipe an old feed mixer and an old belt conveyor to put it together this winter Now he is experimenting feeding the end product to his cattle and using it on crops
“I lucked out when I found a 60-in length of 1/2-in wall 5-ft diameter steel pipe at the local scrap yard ” says Saunders “I mounted the pipe on an old New Holland 352 mixer/mill frame and fabricated up from there ”
The pipe was ideal for his concept He divided it into 3 levels or floors Each floor is actually a removable tray with a hole offset from the one above or below and a rake arm attached to a center shaft
The shaft extends through all 3 floors and is powered by a 1/2 hp variable speed motor at the bottom of the machine A repurposed AC blower pushes air through the hollow shaft to cool it
At the top of the chamber Saunders installed a rotary valve to accept the raw wood as it is delivered by belt The 18-in wide 22-ft long belt conveyer is powered by a 1 hp DC motor with variable speed control When not accepting wood the rotary valve keeps air out of the machine
To start the burn Saunders adds some feedstock to the top level lights it with a propane torch and closes up the chamber The burning material uses up oxygen as it reaches a pyrolysis temperature of 450°F a process that takes about 20 min At that point cellular bonds break which produces more heat Saunders shuts off the torch and starts feeding in fresh wood chips or sawdust As new material enters the old material is swept down to the next level and then to the third level The arms and the conveyor are synchronized so the wood spends the same amount of time on each level
At each level the decomposition continues as volatiles are pulled off to combust and the temperature reaches its target of 1 292 °F
By the time the arm comes around on the third level to sweep it out the process is finished and only charcoal is left behind says Saunders
The time needed can vary depending on the size of material and moisture levels The speed can be adjusted accordingly
The important thing in making biochar is the consistency of the material in its size and moisture levels says Saunders “We could run crop residue through it if it was consistent
If he has the process down for making the biochar Saunders is still proving out its value
Research in Australia and elsewhere shows that cattle fed biochar as a supplement belch less and take in more nutrients says Saunders Feeding biochar to cattle on feed could shave a month off from start to finish in the feedlot
He is also intrigued by the use of biochar in crop production It holds up to 5 times its weight in water One gram of biochar has the surface area of a tennis court Blend it with manure or compost to innoculate it with bacteria and you ve created a slow release fertilizer
I am open to any number of options including helping to build other machines under an agreement on sale of the biochar he says Right now I am ramping up production This machine will have a throughput of more than half a ton per day
Contact: FARM SHOW Followup Bruce Saunders P O Box 871 Millet Alta Canada T0C 1Z0 ph 780 499-9833; bermenergy@gmail com
To read the rest of this story, download this issue below or click
here to register with your account number.