They Moved 60-Ft Silo
For years Ontario farmer Ron Forbes hauled feed from a silo on an adjacent farm to cows 3/4 mile away on his home place. He finally decided to eliminate the time-consuming daily chore by moving the silo across 4,000 ft. of fields to a spot next to his dairy barn.
Forbes used three bulldozers to tow the 60-ft. high, 16-ft. dia. steel-reinforced poured concrete silo on a steel "sled" across corn stalks, wheat stubble, a newly planted wheat field, and a pasture.
"It got a lot of attention. Hundreds of people came out to watch the day we moved it last fall," says Forbes.
He moved the silo with the help of neighbor Tom Gordon, who operates a silo dismantling business and originally came up with the idea of moving the silo.
The men started the job by air-hammering four holes in the bottom of the silo and then using a cement saw to cut 2 ft. off the base of the silo. They used two 50-ton hydraulic jacks to lift the silo up 8 in., knocked out the base, and then put the "sled" underneath. Each side of the sled consists of two 21-ft. long, 18-in. wide steel I-beams welded together side by side with a 1/4-in. thick steel plate welded to the bottom. A pair of 12-in. I-beams ran across on the front and back. A curved steel plate welded underneath the front of the frame keeps it from digging into the ground. They also welded 5/8 by 8-in. angle iron cross braces onto each corner at a 45 degree angle and ran heavy wooden beams from corner to corner to reinforce the frame.
They wrapped a 200-ft. length of 2-in. dia. steel cable around the bottom of the silo and through guides on each side of the sled, then hooked it up to three bulldozers - a Komatsu D155, and a Caterpillar D6 and D7. The cable ran through a big "snatch block" pulley positioned about 80 ft. in front of the silo.
On moving day the bulldozers arrived around 1 p.m. and were hooked up in about a half hour. They moved the silo about 5 in. on the first try, then the bulldozers had to be repositioned to get more traction. The D6 dozer was used as an anchor on one side of the "snatch block", with the D7 and Komatsu pulling together on the other side of the pulley. Once the silo was off its old foundation and in the field it pulled easy and there was no need to use an anchor.
"It wasn't as difficult to move as I had anticipated," says Forbes. "For years I had been using the silo to store high moisture corn and using my pickup to haul feed every day from it to my home farm.
"The silo is in good shape since it's only 17 years old. It cost about $10,000 to move compared to $25,000 to $35,000 for a comparable new concrete silo.
"The hardest part was moving the silo off its foundation. The silo, cable, and sled weighed about 130 tons. Once we got going it slid across the field with amazing ease. We traveled at about 4 mph.
"After the silo was moved onto its new foundation, we used cement saws to cut four 18-in. high, 1-ft. wide holes in the base. We then used two jacks to tip the silo up, one side at a time, so that the sled could be pulled out. Then we made a form around the base and poured three yards of concrete to anchor the silo."
Contact: FARM SHOW Followup, Ron Forbes, RR 3, Ingersoll, Ontario, Canada N5C 3J6 (ph 519 285-3800).
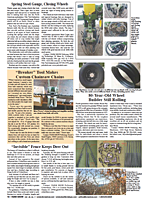
Click here to download page story appeared in.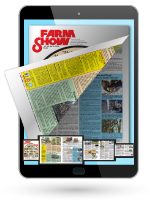
Click here to read entire issue
They Moved 60-Ft Silo AG WORLD Ag World 18-3-19 For years Ontario farmer Ron Forbes hauled feed from a silo on an adjacent farm to cows 3/4 mile away on his home place. He finally decided to eliminate the time-consuming daily chore by moving the silo across 4,000 ft. of fields to a spot next to his dairy barn.
Forbes used three bulldozers to tow the 60-ft. high, 16-ft. dia. steel-reinforced poured concrete silo on a steel "sled" across corn stalks, wheat stubble, a newly planted wheat field, and a pasture.
"It got a lot of attention. Hundreds of people came out to watch the day we moved it last fall," says Forbes.
He moved the silo with the help of neighbor Tom Gordon, who operates a silo dismantling business and originally came up with the idea of moving the silo.
The men started the job by air-hammering four holes in the bottom of the silo and then using a cement saw to cut 2 ft. off the base of the silo. They used two 50-ton hydraulic jacks to lift the silo up 8 in., knocked out the base, and then put the "sled" underneath. Each side of the sled consists of two 21-ft. long, 18-in. wide steel I-beams welded together side by side with a 1/4-in. thick steel plate welded to the bottom. A pair of 12-in. I-beams ran across on the front and back. A curved steel plate welded underneath the front of the frame keeps it from digging into the ground. They also welded 5/8 by 8-in. angle iron cross braces onto each corner at a 45 degree angle and ran heavy wooden beams from corner to corner to reinforce the frame.
They wrapped a 200-ft. length of 2-in. dia. steel cable around the bottom of the silo and through guides on each side of the sled, then hooked it up to three bulldozers - a Komatsu D155, and a Caterpillar D6 and D7. The cable ran through a big "snatch block" pulley positioned about 80 ft. in front of the silo.
On moving day the bulldozers arrived around 1 p.m. and were hooked up in about a half hour. They moved the silo about 5 in. on the first try, then the bulldozers had to be repositioned to get more traction. The D6 dozer was used as an anchor on one side of the "snatch block", with the D7 and Komatsu pulling together on the other side of the pulley. Once the silo was off its old foundation and in the field it pulled easy and there was no need to use an anchor.
"It wasn't as difficult to move as I had anticipated," says Forbes. "For years I had been using the silo to store high moisture corn and using my pickup to haul feed every day from it to my home farm.
"The silo is in good shape since it's only 17 years old. It cost about $10,000 to move compared to $25,000 to $35,000 for a comparable new concrete silo.
"The hardest part was moving the silo off its foundation. The silo, cable, and sled weighed about 130 tons. Once we got going it slid across the field with amazing ease. We traveled at about 4 mph.
"After the silo was moved onto its new foundation, we used cement saws to cut four 18-in. high, 1-ft. wide holes in the base. We then used two jacks to tip the silo up, one side at a time, so that the sled could be pulled out. Then we made a form around the base and poured three yards of concrete to anchor the silo."
Contact: FARM SHOW Followup, Ron Forbes, RR 3, Ingersoll, Ontario, Canada N5C 3J6 (ph 519 285-3800).
To read the rest of this story, download this issue below or click
here to register with your account number.