Frustrating Harvest Produced Innovative Cutting System
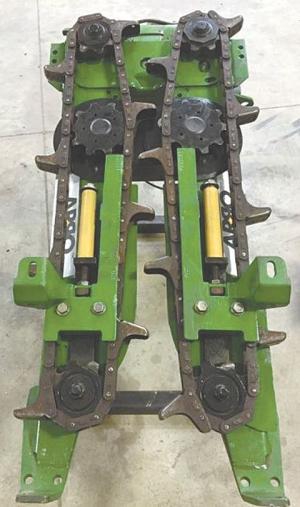 ✖  |
In 2015 custom harvester Randy Burns was frustrated by poor header performance as he harvested lodged milo. Meanwhile, his son-in-law, Kansas farmer Kyle Kopper, was looking for a way to lower machinery costs and get more consistent residue management for no till planting.
About the same time, Alan VanNahmen, a former engineer for Deere, was looking for an improved header for cellusolic ethanol crops. The Kansas trio teamed up to design, build, and patent an alternative rotary row crop harvesting system called ARRO®. The device retrofits to existing corn heads and achieves effective milo, millet, sunflower, corn, and bio-mass crop harvesting. In three years more than 100 of the ARRO units have been installed, and cutters who’ve used them say they’re getting more bushels per hour without as much material going through the combine.
Kopper says that after the ARRO system is installed, cutting height can be adjusted to leave 12 in. or more of stubble on the ground. “That preserves moisture while reducing wind and water erosion, providing a good setup for future no till planting.” Kopper says the system is also an inexpensive way to achieve better harvesting results without investing in a new or specialized cutting head.
Cornhead components including the chain drives, gear case, row unit slip clutches, poly center shields and divider points are left in place when the ARRO system is put on. Installation is done by removing the existing trash knives, stalk rolls and stalk roll shaft housings. Stalk guides for the ARRO system are bolted in place of trash knives on some corn head models. Gear case cover plates are bolted onto front-of-row-unit gearcases while front chain idlers, chain guides and deck plates are removed.
Two new holes in the row unit frame bolt the ARRO sprocket-disc assemblies in place. Front deck plate spacers and chain tensioners are reinstalled and adjusted for the crop being harvested.
ARRO units currently retrofit several Deere, CaseIH and New Holland heads. VanNahmen says test units and validation should be completed for Claas and Gleaner corn heads during fall, 2018. Shield Agriculture Equipment of Hutchinson, Kan. is the authorized distributor and several Deere and Case IH dealers in the High Plains sorghum belt are dealer/installers.
Beause of its unique harvesting characteristics, VanNahmen says the ARRO is also being used to harvest lettuce seed, industrial hemp stalk fiber and seeds, and on forage cutters to harvest sorghum “headlage”. An ARRO3 version with expanded capabilities is under additional patent pending development.
Long time Oklahoma farmer JB Stewart says he’s waited 50 years for something this effective, a product that co-developer VanNahmen says “makes harvesting fun again.”
Contact: FARM SHOW Followup, Kopper Kutter LLC, 10602 State Road 23, Cimarron, Kansas 67835 (ph 620 855-2988; ARRO@KopperKutter.com).
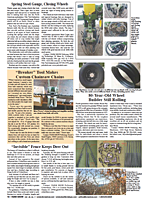
Click here to download page story appeared in.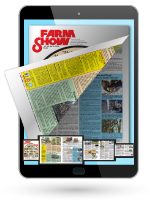
Click here to read entire issue
Frustrating Harvest Produced Innovative Cutting System COMBINES Accessories In 2015 custom harvester Randy Burns was frustrated by poor header performance as he harvested lodged milo Meanwhile his son-in-law Kansas farmer Kyle Kopper was looking for a way to lower machinery costs and get more consistent residue management for no till planting About the same time Alan VanNahmen a former engineer for Deere was looking for an improved header for cellusolic ethanol crops The Kansas trio teamed up to design build and patent an alternative rotary row crop harvesting system called ARRO® The device retrofits to existing corn heads and achieves effective milo millet sunflower corn and bio-mass crop harvesting In three years more than 100 of the ARRO units have been installed and cutters who’ve used them say they’re getting more bushels per hour without as much material going through the combine Kopper says that after the ARRO system is installed cutting height can be adjusted to leave 12 in or more of stubble on the ground “That preserves moisture while reducing wind and water erosion providing a good setup for future no till planting ” Kopper says the system is also an inexpensive way to achieve better harvesting results without investing in a new or specialized cutting head Cornhead components including the chain drives gear case row unit slip clutches poly center shields and divider points are left in place when the ARRO system is put on Installation is done by removing the existing trash knives stalk rolls and stalk roll shaft housings Stalk guides for the ARRO system are bolted in place of trash knives on some corn head models Gear case cover plates are bolted onto front-of-row-unit gearcases while front chain idlers chain guides and deck plates are removed Two new holes in the row unit frame bolt the ARRO sprocket-disc assemblies in place Front deck plate spacers and chain tensioners are reinstalled and adjusted for the crop being harvested ARRO units currently retrofit several Deere CaseIH and New Holland heads VanNahmen says test units and validation should be completed for Claas and Gleaner corn heads during fall 2018 Shield Agriculture Equipment of Hutchinson Kan is the authorized distributor and several Deere and Case IH dealers in the High Plains sorghum belt are dealer/installers Beause of its unique harvesting characteristics VanNahmen says the ARRO is also being used to harvest lettuce seed industrial hemp stalk fiber and seeds and on forage cutters to harvest sorghum “headlage” An ARRO3 version with expanded capabilities is under additional patent pending development Long time Oklahoma farmer JB Stewart says he’s waited 50 years for something this effective a product that co-developer VanNahmen says “makes harvesting fun again ” Contact: FARM SHOW Followup Kopper Kutter LLC 10602 State Road 23 Cimarron Kansas 67835 ph 620 855-2988; ARRO@KopperKutter com
To read the rest of this story, download this issue below or click
here to register with your account number.