Self-Driving Tractor Handles Many Fieldwork Jobs
Idaho brothers Dave and Bill Farb weren’t satisfied with how autosteer technology worked on their farm, so instead of trying and buying a different system, they built their own. Using their background as CAD software engineers they designed and built the “Farb-E”, a custom-made power unit that uses a diesel motor running a hydraulic system powering two small tracks.
Dave Farb says the prototype operated like a skid steer without a cab and it worked well, pulling equipment across a field in a designated pattern, controlled by GPS. The project gave them additional ideas, which they used for integrating the autonomous software into a CAT 259D skidsteer. That platform has now logged more than 1,000 hrs. on 5 different machines, handling heavy disking, cultivating, harrowing, seeding, spraying and soil sampling. Machines have worked on fields ranging in size from 5 to several hundred acres. Development on their machines has involved equipment, expertise and products from nearly 10 different ag technology companies.
In the summer of 2018 Dave Farb demonstrated the autonomous system on a 100 hp. Caterpillar 299D2 Track Loader at a Wisconsin farm show. The machine pulls and communicates with any hitch-type or 3-point implement. Farb says his company’s driverless technology uses sophisticated software that pairs the skid steer’s control system with GPS guidance. Using the hydrostatic drive they regulate the speed, direction and steering from a single control point, which can be a computer, tablet or smartphone. Implement controls are also handled with the system.
Farb engineer Jordan Schwers says that running the units in repetitious field operations has allowed them to identify issues that affect operation, then create solutions that can be handled with sensors. “We’ve taken the approach of automating through seeking out mistakes, knowing that experiencing the problems is the best way to create a good solution,” Schwers says.
Farb says they used a hydrostatic power unit rather than a conventional tractor because the hydrostatic machine was easier to make driverless. A tractor would’ve required controls for the transmission, engine, steering, braking and clutching.
Farb envisions selling vehicles equipped with the technology and also offering them as a contract service, where a farmer would pay a per-acre fee comparable to custom rates in his area.
Contact: FARM SHOW Followup, Farb
Guidance Systems, Post Falls, Idaho (www.farbgs.com).
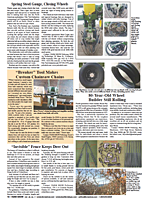
Click here to download page story appeared in.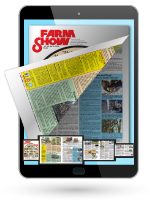
Click here to read entire issue
Self-Driving Tractor Handles Many Fieldwork Jobs TRACTORS Miscellaneous Idaho brothers Dave and Bill Farb weren’t satisfied with how autosteer technology worked on their farm so instead of trying and buying a different system they built their own Using their background as CAD software engineers they designed and built the “Farb-E” a custom-made power unit that uses a diesel motor running a hydraulic system powering two small tracks Dave Farb says the prototype operated like a skid steer without a cab and it worked well pulling equipment across a field in a designated pattern controlled by GPS The project gave them additional ideas which they used for integrating the autonomous software into a CAT 259D skidsteer That platform has now logged more than 1 000 hrs on 5 different machines handling heavy disking cultivating harrowing seeding spraying and soil sampling Machines have worked on fields ranging in size from 5 to several hundred acres Development on their machines has involved equipment expertise and products from nearly 10 different ag technology companies In the summer of 2018 Dave Farb demonstrated the autonomous system on a 100 hp Caterpillar 299D2 Track Loader at a Wisconsin farm show The machine pulls and communicates with any hitch-type or 3-point implement Farb says his company’s driverless technology uses sophisticated software that pairs the skid steer’s control system with GPS guidance Using the hydrostatic drive they regulate the speed direction and steering from a single control point which can be a computer tablet or smartphone Implement controls are also handled with the system Farb engineer Jordan Schwers says that running the units in repetitious field operations has allowed them to identify issues that affect operation then create solutions that can be handled with sensors “We’ve taken the approach of automating through seeking out mistakes knowing that experiencing the problems is the best way to create a good solution ” Schwers says Farb says they used a hydrostatic power unit rather than a conventional tractor because the hydrostatic machine was easier to make driverless A tractor would’ve required controls for the transmission engine steering braking and clutching Farb envisions selling vehicles equipped with the technology and also offering them as a contract service where a farmer would pay a per-acre fee comparable to custom rates in his area Contact: FARM SHOW Followup Farb Guidance Systems Post Falls Idaho www farbgs com
To read the rest of this story, download this issue below or click
here to register with your account number.