You have reached your limit of 3 free stories. A story preview is shown instead.
To view more stories
(If your subscription is current,
click here to Login or Register.)
She Turns Dairy Manure Into Fuel
Rose Marie Belforti turns excess dairy cattle manure into burnable bricks. A mixture of manure and bedding is compressed, dried and stored until needed.
“We’ve burned them in an inside fireplace, a wood stove and in an outside fireplace,” says Belforti. “They burn with no animal smell, with a scent a bit lik
..........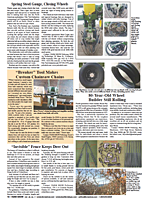
You must sign in, subscribe or renew to see the page.
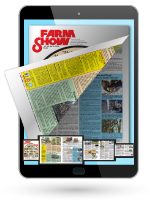
You must sign in, subscribe or renew to see the flip-book
She Turns Dairy Manure Into Fuel DAIRY EQUIPMENT & IDEAS Rose Marie Belforti turns excess dairy cattle manure into burnable bricks A mixture of manure and bedding is compressed dried and stored until needed “We’ve burned them in an inside fireplace a wood stove and in an outside fireplace ” says Belforti “They burn with no animal smell with a scent a bit like incense It’s a good use of what is often considered waste ” Belforti has been making fuel from her well-bedded dairy cattle manure for years Until recently she would hand press it then put the bricks on boards and let them dry “You can use the small hand-pressed pieces like kindling but if you want larger tighter bricks you need a press ” A couple of years ago Belforti got serious with her dairy manure fuel She applied for and received a Farmer Grant from the Northeast Sustainable Agriculture Research and Education Program SARE The grant was for making a hydraulic manure press scaled for small farm use Belforti worked with Chris Callahan a technical advisor from the University of Vermont and Steve Lonsky a local welder They came up with a press chamber that will produce a 7 by 9 by 9-in briquette with a dry weight of approximately 4 lbs The 3 000 psi 5-in bore 24-in reach hydraulic cylinder and pump are powered by a Honda OHV 270cc 8 1/2 hp engine “The press could easily be made from a modified log splitter ” notes Belforti Equipment and materials totaled just under $2 400 and labor ran $3 662 for the prototype Details on the make and the testing can be found at the SARE and FarmHacks websites below Once completed Belforti began working on what became her biggest challenge a good “recipe” She tested different ratios of fresh manure and manure/bedding straw and wood shavings to come up with a mix that pressed well and dried efficiently with reasonable density “The criteria for excellence is that the briquette must hold together so it can be handled and set to dry ” says Belforti “If too moist it won’t survive the pressing; if too dry or not well mixed it will crumble during handling ” When she began making briquettes Belforti quickly discovered that gaps in the press chamber were a problem Under full compression too much material was pushed out of the box not just the excess water After trying various fixes Belforti found that inserting a composite shingle and fabric screening at the end of the chamber held the solids while allowing the liquid to be pressed out She also discovered that a piece of tarp over the top as a brick was being pressed prevented what she described as “manure rain ” Once the bricks are pressed Belforti places them on racks in a single layer to dry under roof for several weeks The closer to 100 percent moisture-free the higher the btu value in the brick At 10 5 percent moisture she estimates a brick will produce 6 841 btu’s per pound “Typically they should dry in a greenhouse or hoop house with good air flow ” says Belforti “They need to be turned or have a fan on them ” Using the press Belforti was able to produce an average of thirty 3-lb bricks per hour for press operating costs of $2 10 Although Belforti reduced her herd size when moving to a smaller acreage in Texas she continues to make manure bricks “I wanted to see if it was worth it to make a press and it was ” she says Contact: FARM SHOW Followup Rose Marie Belforti 92 Himmel Rd Fredericksburg Texas 78624 ph 315 406-2894; himmelhaus92@gmail com or https://projects sare org/sare_project/fne17-862/ or www farmhack org/tools/livestock-manure-fuel-briquetter-biobeast
To read the rest of this story, download this issue below or click
here to register with your account number.