You have reached your limit of 3 free stories. A story preview is shown instead.
To view more stories
(If your subscription is current,
click here to Login or Register.)
Sawdust Spreader Converted To Handle Compost
Ian Wyndlow converted a 3-pt. mounted sawdust spreader to lay compost down in vegetable crops. Initially, he used it to broadcast compost over a 45-ft. span to the side of the spreader.
“We have 15 acres of organic vegetable production, which we sell at a local farmer’s market and to 70 CSA members, as w
..........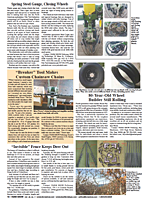
You must sign in, subscribe or renew to see the page.
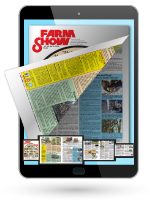
You must sign in, subscribe or renew to see the flip-book
Sawdust Spreader Converted To Handle Compost MANURE HANDLING Miscellaneous Ian Wyndlow converted a 3-pt mounted sawdust spreader to lay compost down in vegetable crops Initially he used it to broadcast compost over a 45-ft span to the side of the spreader “We have 15 acres of organic vegetable production which we sell at a local farmer’s market and to 70 CSA members as well as to local restaurants ” says Wyndlow “We wanted to find a way to lay compost directly onto the seedbeds where we need it ” Originally a hydraulic cylinder attached to the top link on the spreader’s 3-pt hitch allowed the 4-ft wide hopper to tilt back 90° to scoop up material When full of compost the hopper was too heavy for my tractor hydraulics to lift it back into place plus I needed more weight on the front end says Wyndlow The compost also bridged on the walls especially if it was a little moist The spreader needed to be modified Part of the bridging problem came from the sides not being steep enough to allow the compost to slide Wyndlow welded a plate inside the hopper that reduced the volume about 20 percent and made for a much steeper wall This in turn reduced potential weight and improved compost flow In order to lay the compost over the bed instead of broadcasting it to one side Wyndlow removed the impeller with its pto drive and closed off the opening replacing it with a hopper-wide slot at the bottom of the rear panel He also attached metal sheets to either side of the slot to further compress the flow to bed width Wyndlow removed the auger that fed the impeller but retained the hydraulic motor that powered it With the help of Ben his 11-year old son he replaced the auger with a beater Ben welded tabs on a piece of pipe that we mounted in place of the auger says Wyndlow He also helped with welding tabs on a rail that I installed below the slot The tabs support a flap of rubber that blocks the flow of compost The rail is hinged to the spreader Two pipes connected at right angles to each other extend from the rail up and then forward to the driver s reach The pipe has a series of stops on it that keep it partially open when running and closed in transit explains Wyndlow As the beater turns it pushes compost out of the slot A second beater installed above it helps further reduce bridging A roller chain from a sprocket on the lower beater drives the upper beater The upper beater as well as bearings shafts gears and drive chain were salvaged and repurposed from an old Deere silage box says Wyndlow The only new component was a hydrostatic valve plumbed to run the rotation of the beaters or the tipping motion of the hopper Contact: FARM SHOW Followup Ian Wyndlow 13188 Doole Rd Ladysmith B C Canada V9G 1G6 ph 250 619-9760; ian@liquidstonestudios com
To read the rest of this story, download this issue below or click
here to register with your account number.