You have reached your limit of 3 free stories. A story preview is shown instead.
To view more stories
To view more stories
SUBSCRIBE OR RENEW NOW
(If your subscription is current, click here to Login or Register.)1979 - Volume #3, Issue #3, Page #14
[ Sample Stories From This Issue | List of All Stories In This Issue]
Whole Crop Harvesting
Swedish 'all-in' harvesting system will challenge the supremacy of the combine by: Clearing corn fields in one pass
Continuing to work independently of the weather
Eliminating grain losses and straw handling
Making economic use of all parts of the crop
&..........
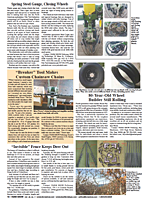
You must sign in, subscribe or renew to see the page.
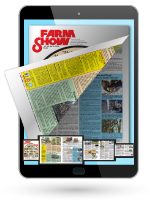
You must sign in, subscribe or renew to see the flip-book
Whole Crop Harvesting CROPS New Techniques 3-3-14 Swedish 'all-in' harvesting system will challenge the supremacy of the combine by:
Clearing corn fields in one pass
Continuing to work independently of the weather
Eliminating grain losses and straw handling
Making economic use of all parts of the crop
Converting bulk fiber to marketable pellet form
Adapting to green crop dehydration and fractionation
Increasing the potential range of crop varieties and types
Extending the cropping and harvesting season
Expanding farm production to serve other industries
Securing sufficient extra yield to pay for itself
Motor up to the small town of Kopingebro at the southern tip of Sweden and one of the first things you will see is the world's second and largest commercial plant for drying and processing whole crops.
The Swedish Sugar Co. is investing $4 million in its construction. It will take cereal crops from some 10,000 acres of surrounding farmland and dry it at the rate of 30 tons per hour.
The project is the result of some revolutionary thinking about harvesting by Ingemar Bjurenvall, President of Kockums Construction AB, Hoganas, Sweden, which is supplying and erecting the plant. Its design is based on experience gained with a pilot installation having one-third of the capacity (10 tons/hr.) built and operated by the company over the past two seasons at Hogesta.
The argument for whole crop harvesting rests on its efficiency as an energy system. The objective is to harness the power of the sun, utilizing all the products of photosynthesis and wasting nothing: Put it how you will, it means exploiting to the full what is sometimes called the biomass - that reservoir of energy created by the sun out of soil, air and water.
Kockums' whole crop harvesting process can be broken down into three stages:
The harvester: In essence this is a self-propelled forage harvester but, because the economy of the system
depends upon harvesting 24 hours a day, conventional machines are of no use.
Kockums' harvester, although based on an American model, has been redesigned and strengthened to stand up to continuous operation. It has a 250 h.p. engine, articulated steering, all-hydrostatic drives and transmission to four equal-sized wheels with wide-tread tires, a cylinder chopper and alternative quick-attach direct-cut, pick-up and row-crop headers.
The machine is expected to cost $121,000, but its daily output will be up to 10 times that of a large combine. In addition its use will not be restricted to the harvesting of cereals.
Transport: An established system is employed on the harvester and transport trucks for setting down and picking up the containers. It consists of_a hydraulically actuated arm and hook designed to engage a lug on one end of the container, which rides on rollers as it comes on and off the vehicle.
Drying and processing: A new type of rotary drum drier has been developed, employing lower temperatures and a longer run than a conventional grass drier. At Kopingebro, three different burners are available to suit the nature of the incoming material.
Apart from the ease and efficiency of grain separation during the drying process, an outstanding advantage of the plant is its ability to separate the remainder of the crop into different and highly individual fractions.
The implications of switching from combine to whole crop harvesting are, of course, enormous. For a start, take the harvester itself. Kockums point out that its whole crop machine does a simple, straightforward job at high speed, regardless of the weather.
The whole crop harvester is also equally capable of handling fresh or wilted green crops, just like a conventional forage harvester. This means that its capital and operating costs, in common with those of the whole system, can be spread over both forage and cereals harvests.
It is the implications of the processing plant, however, that are the most far-reaching. In the first place, it is a grain drier, capable of relieving the farmer of the need to dry, clean and store his grai
To read the rest of this story, download this issue below or click here to register with your account number.