He Turns Harvestores Into Conventional Silos
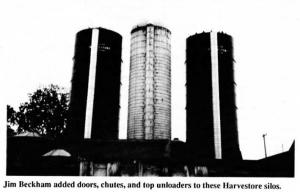 ✖  |
"It's the best ground-breaking machine I've ever seen. Last winter I tested it on frozen ground. It worked up the ground so well it was ready to plant in the spring," says Ernest Gerber, Coronation, Alberta, about his home-built 140-rpm giant "rotovator" that he uses to break fallow ground or to bring new land into production.
The rotovator consists of two 5-ft. dia. steel discs, mounted together on truck rims and fitted with big industrial tiller teeth. The pto-driven tiller discs churn through soil down to 13 in. deep, and chew through trees up to 3 in, dia. Gerber says it'll even turn up rocks up to 24 in. dia. After one pass at speeds up to 6 mph, the soil is ready to plant.
"It leaves a smooth, even seedbed. You almost can't believe what a beautiful job it does," says Gerber, who got the idea for the machine from big industrial tillers that are 6 or 7 ft. wide but not as big in diameter as his machine. The industrial machines are used to tear up gravel or asphalt road beds and for other heavy tillage chores. In Gerber's area, farmers sometimes rent the industrial ma-chines to work new ground. He doesn't like the machines, however.
"They turn to the back so they push the tractor forward. You need a big 4-WD tractor just to hold them back. Also, they run at up to 900 rpm's and go only 6 in. deep, and they require extra motors to drive them. My machine turns counter-clockwise and cuts 13 in. deep using only a tractor pto and about a 150 hp. tractor," says Gerber.
He cut the 5-ft. dia. tiller discs out of 1-in. thick steel plate. The big discs are welded to wheel rims off a 3-ton truck and mounted side-by-side on a heavy-duty truck rear end. Each disc is fined with 36 tiller teeth facing alternate directions. The double set of tiller discs cut a strip 20 in. wide. Gerber can remove some of the teeth to reduce the width to 10 in. if needed for digging trenches for cable or pipe. The self-sharpening teeth cost $8 apiece and are made to fit industrial tillers. After 3 years of use Gerber says he's yet to replace any teeth.
The tractor pto direct-drives the truck rear end. Gerber "rubber cushioned" the hookup between the pto and rear end drive-shaft using rubber belting. He can shift the 2-speed rear end between high and low to turn the tiller discs at either 140 or 180 rpm's. The rear end and tiller is raises and lower hydraulically on loose lengths of chain that allows the tiller to "jump" up when it hits a rock or other obstacle.
Gerber pulls the rotovator with a 2470 Case. "I've never plugged it.' At 6 in. deep I can run at 5 to 6 mph. When you run over trees or brush, you have to slow down to chew them up. A large metal shield protects the tractor and the operator from dirt and debris thrown up by the machine. It takes a while to break new ground but it does such a great job you can plant into it after one pass with the machine," says Gerber, who spent less than $1,000 to build the machine.
Contact: FARM SHOW Followup, Ernest Gerber, Box 158, Coronation, Alberta T0C 1C0 Canada (ph 415 578-4180 or 578-2194).
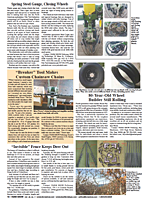
Click here to download page story appeared in.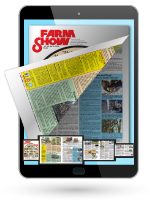
Click here to read entire issue
He Turns harvestores into Conventional Silos CROP STORAGE Silos (50) 13-5-27 "It's the best ground-breaking machine I've ever seen. Last winter I tested it on frozen ground. It worked up the ground so well it was ready to plant in the spring," says Ernest Gerber, Coronation, Alberta, about his home-built 140-rpm giant "rotovator" that he uses to break fallow ground or to bring new land into production.
The rotovator consists of two 5-ft. dia. steel discs, mounted together on truck rims and fitted with big industrial tiller teeth. The pto-driven tiller discs churn through soil down to 13 in. deep, and chew through trees up to 3 in, dia. Gerber says it'll even turn up rocks up to 24 in. dia. After one pass at speeds up to 6 mph, the soil is ready to plant.
"It leaves a smooth, even seedbed. You almost can't believe what a beautiful job it does," says Gerber, who got the idea for the machine from big industrial tillers that are 6 or 7 ft. wide but not as big in diameter as his machine. The industrial machines are used to tear up gravel or asphalt road beds and for other heavy tillage chores. In Gerber's area, farmers sometimes rent the industrial ma-chines to work new ground. He doesn't like the machines, however.
"They turn to the back so they push the tractor forward. You need a big 4-WD tractor just to hold them back. Also, they run at up to 900 rpm's and go only 6 in. deep, and they require extra motors to drive them. My machine turns counter-clockwise and cuts 13 in. deep using only a tractor pto and about a 150 hp. tractor," says Gerber.
He cut the 5-ft. dia. tiller discs out of 1-in. thick steel plate. The big discs are welded to wheel rims off a 3-ton truck and mounted side-by-side on a heavy-duty truck rear end. Each disc is fined with 36 tiller teeth facing alternate directions. The double set of tiller discs cut a strip 20 in. wide. Gerber can remove some of the teeth to reduce the width to 10 in. if needed for digging trenches for cable or pipe. The self-sharpening teeth cost $8 apiece and are made to fit industrial tillers. After 3 years of use Gerber says he's yet to replace any teeth.
The tractor pto direct-drives the truck rear end. Gerber "rubber cushioned" the hookup between the pto and rear end drive-shaft using rubber belting. He can shift the 2-speed rear end between high and low to turn the tiller discs at either 140 or 180 rpm's. The rear end and tiller is raises and lower hydraulically on loose lengths of chain that allows the tiller to "jump" up when it hits a rock or other obstacle.
Gerber pulls the rotovator with a 2470 Case. "I've never plugged it.' At 6 in. deep I can run at 5 to 6 mph. When you run over trees or brush, you have to slow down to chew them up. A large metal shield protects the tractor and the operator from dirt and debris thrown up by the machine. It takes a while to break new ground but it does such a great job you can plant into it after one pass with the machine," says Gerber, who spent less than $1,000 to build the machine.
Contact: FARM SHOW Followup, Ernest Gerber, Box 158, Coronation, Alberta TOC 1 CO Canada (ph 415 578-4180 or 578-2194).
To read the rest of this story, download this issue below or click
here to register with your account number.