2020 - Volume #44, Issue #4, Page #38
[ Sample Stories From This Issue | List of All Stories In This Issue | Print this story
| Read this issue]
Autonomous Tractor Adapts Fast
![]() |
“We’ve been working on the Erion for 2 years,” says Marc-Antoine Legault, Innovation Vehicle Institute. “We hope to have 10 units in farm fields by 2121.”
The 2 1/2-ton, 30-hp. tractor features 9 electric motors with gearboxes. Each wheel has a drive motor as well as a motor for steering. The ninth motor raises and lowers the undercarriage tool. Electric actuators control row width, moving the side rails of the tractor frame apart or closer together, changing wheel spacings from 54 in. to 78 in. in seconds.
“The steering motors can work in tandem or independently for any type of steering desired,” says Legault. “The tractor can turn on a dime, crab steer or shift to one side or the other.”
A 350-volt battery on the trailer that delivers the tractor to the field can recharge on-board batteries, lengthening the workday without having to go back to the shop.
The design of the tractor was the result of interviews with farmers from different sized operations. “Weeding vegetable crops kept coming up so we focused on that,” says Legault. “It is labor intensive, and farmers have turned to ever-larger tractors to speed up the work. The resulting soil compaction is reducing yields. Autonomous tractors can deploy smaller equipment.”
He explains that the combination of mobility with undercarriage mounting of tools, such as cultivators, will allow more precise and close-to-the-row fieldwork. The prototype has been fitted with a 6-ft. wide cultivator, but is capable of carrying a 12-ft. wide attachment.
“Our first application is weeding with the cultivator,” says Legault. “Other types of fieldwork are just a matter of adapting attachments to the frame.”
The undercarriage tools require a strong framework. The heavy-duty joints are specifically designed to handle the forces produced by attachments.
The tractor can be controlled remotely as it leaves a trailer to enter a field. Once in the field, the autonomous mode relies on the on-board computer and sensors. Cameras and AI algorithms will detect plants and manage where the cultivation tools go within the row. The system is designed to communicate with a control communicator at a base station with human intervention only as needed.
“RTK GPS is our navigation base,” says Legault. “We are also using Lidar to detect obstacles and 3D lasers, looking for the best configuration of both systems as we experiment in the field.”
A bird’s-eye camera has also been added to transmit activity real time to the base. This will allow the technician in charge to understand what is going on around the tractor, explains Legault.
“As we gain experience and confidence, we will better understand any safety concerns,” he says. “We will start with something simple like cultivating and data gathering and then follow that with real-life experience.”
IVI is working with Elmec, a Quebec company, on the project. Funding has also come from the provincial and federal governments. Elmec’s concept is to provide field services such as cultivation to farmers for a fee, rather than producing and selling the final autonomous product.
Other projects of IVI include an all-electric school bus, an urban transit bus, and an electric delivery vehicle.
Contact: FARM SHOW Followup, Innovative Vehicle Institute, 25 boulevard Maisonneuve, Saint-Jérôme, Quebec Canada J5L 0A1 (ph 450 431-5744; malegault@ivisolutions.ca; www.ivisolutions.ca).
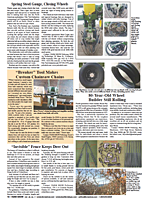
Click here to download page story appeared in.
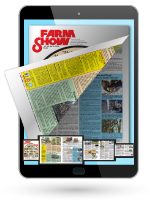
Click here to read entire issue
To read the rest of this story, download this issue below or click here to register with your account number.