You have reached your limit of 3 free stories. A story preview is shown instead.
To view more stories
(If your subscription is current,
click here to Login or Register.)
He Makes His Own Fuel With On-Farm Biodiesel Plant
Shannon Nickolay grows his own tractor fuel. His simple production system produces fuel, feed for his cattle, and adds a crop to his corn and soybean rotation. From May through September he burns mostly homemade fuel in his diesel-powered equipment.
“It only takes a few minutes a day to make biodiesel at a cost
..........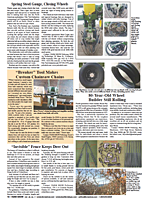
You must sign in, subscribe or renew to see the page.
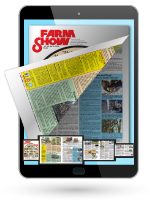
You must sign in, subscribe or renew to see the flip-book
He Makes His Own Fuel With On-Farm Biodiesel Plant ENERGY Alternative Fuels Shannon Nickolay grows his own tractor fuel His simple production system produces fuel feed for his cattle and adds a crop to his corn and soybean rotation From May through September he burns mostly homemade fuel in his diesel-powered equipment “It only takes a few minutes a day to make biodiesel at a cost of about $1 75 per gal ” says Nickolay “When we started in 2006 diesel fuel was pushing $4 per gal and the equipment paid for itself quickly Even today it’s saving us money ” Faced with high fuel prices Nickolay read about a Wisconsin man who was making biodiesel The man shared his experience with him and helped set him up with needed equipment selling him a German-made Comet press Nickolay had a local metal fabricator make a 400-gal reactor with pumps and heater “The only problem with the press is getting parts from Germany when pieces wear out ” he says “The guy I bought my press from is getting out of the business so I have to find a new supplier ” Nickolay keeps wear to a minimum by using “sacrificial” belts Although the press gearbox has a double pulley drive Nickolay uses only one belt and tightens it down “If a piece of bearing or something enters the press the belt will burn out before the chrome-plated parts get scratched ” he explains “Once the chrome is scratched it wears much faster ” Nickolay avoids using soybeans in part because of their low oil content but also to avoid rocks and dirt picked up by the combine Instead he plants about 100 acres of sunflowers and about 40 acres of canola each spring Seed is pressed in 50-bushel batches with sunflower seed producing about 50 to 60 gal of oil per batch and canola seed producing 90 gal of oil per batch While the meal is pushed off to the side for use in Nickolay’s cattle ration the oil is collected in a large plastic tank Most of the sediment in the oil drops out as the oil enters the tank Once a day the oil is pumped to a second plastic tank where it settles over a 5-day period “The sediment from the first tank is fed to young stock by the bucket full ” says Nickolay “They will follow me through the yard for it ” Oil at the top of the second tank gets pumped into a 400-gal stainless steel reactor tank He heats the oil to 120 degrees Nickolay adds about 15 1/2 lbs of potassium hydroxide flakes to 30 to 35 gal of methanol Sunflower oil gets a little more potassium hydroxide while canola gets a little less Once the flakes are dissolved the methanol solution is pumped into the reactor tank Pumps on the bottom of the tank recirculate the methanol-oil mix to the top of the tank for about a 3-hr period Nickolay leaves it in the reactor for a day or so This allows glycerin a byproduct to settle out with more settling out while the biodiesel is in storage Nickolay estimates getting about 35 gal of glycerin per batch of fuel When he has collected about 300 gal or so from storage tanks he heats it up and pushes air through it “I reclaim about 50 gal of methanol per batch for reuse in the reactor ” says Nickolay The biodiesel is pumped into the farm’s 10 000-gal fuel barrel or into smaller plastic totes “We pump the biodiesel off the top of the tanks as we need it ” says Nickolay “We burn the oil straight in older equipment but mix it 50:50 with diesel fuel for use with engines 2005 and newer ” He explains that fuel filters on the newer equipment are too tight to allow the biodiesel molecules through “The equipment does require an up-front investment but if you have the land to produce your own seed and cattle to feed the meal to the cost to produce biodiesel drops pretty fast ” says Nickolay Contact: FARM SHOW Followup Shannon Nickolay D2186 Cty Rd C Stratford Wis 54484 ph 715 305-4735; charity nikolay@yahoo com
To read the rest of this story, download this issue below or click
here to register with your account number.