You have reached your limit of 3 free stories. A story preview is shown instead.
To view more stories
(If your subscription is current,
click here to Login or Register.)
He Makes Knives From Sawmill Blades
Bruce Godlesky uses saw blades and other new and recycled metals to forge his Damascus steel knives. But to ensure quality, he doesn’t use just any metal.
“I have access to a chem-lab to get steels tested. All steels have different properties,” says the Apollo, Penn., knife maker, who avoids metal that doesn
..........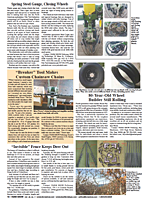
You must sign in, subscribe or renew to see the page.
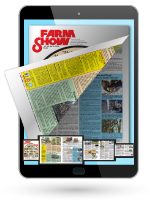
You must sign in, subscribe or renew to see the flip-book
He Makes Knives From Sawmill Blades FARM HOME Miscellaneous Bruce Godlesky uses saw blades and other new and recycled metals to forge his Damascus steel knives But to ensure quality he doesn’t use just any metal “I have access to a chem-lab to get steels tested All steels have different properties ” says the Apollo Penn knife maker who avoids metal that doesn’t have enough carbon “High carbon steel is very attractive and gives you a good cutting tool ” For example the 8-in wide bandsaw blades he uses are high in carbon and nickel Big round 52-in sawmill blades that he has cut into strips with a plasma cutter have high nickel and chromium content so the metal stays shiny He also has a power hammer to flatten 6-sided rod and cable used by the gas industry in his region Damascus knife-making is a process of layering steel that’s forge welded and manipulated to get a pattern Mixing different steel adds to the texture and design For example the shiny parts of his knives are from circular sawblades while the dark lines come from steel such as 1095 tool steel “I make full tang knives with the steel going all the way through the handle and hidden tang knives that narrow down and are epoxied so they are strong All are tested My last test is to chop through deer antlers with them If they don’t chip or crack they are good to go ” Godlesky says Besides the blades Godlesky makes handles out of native woods such as curly maple and walnut and he does his own leatherwork for sheaths and scabbards He doesn’t do custom orders but has a variety of items on sale on his website Contact: FARM SHOW Followup Bruce Godlesky 1002 School Rd Apollo Penn 15613 ph 724 840-5786; brucegodlesky@yahoo com
To read the rest of this story, download this issue below or click
here to register with your account number.