You have reached your limit of 3 free stories. A story preview is shown instead.
To view more stories
(If your subscription is current,
click here to Login or Register.)
Robotic Sorter Helps Harvest In Orchard
A new robotic apple harvester sorts apples in the field as they are picked. The harvester was designed by Michigan State University researchers and built by Precise Manufacturing with funding from the USDA and the Michigan Apple Committee. The in-field sorting harvester is just the first step in a fully robotic apple h
..........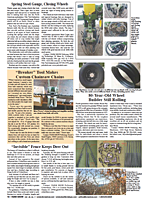
You must sign in, subscribe or renew to see the page.
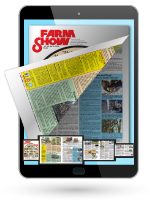
You must sign in, subscribe or renew to see the flip-book
Robotic Sorter Helps Harvest In Orchard CROPS Miscellaneous A new robotic apple harvester sorts apples in the field as they are picked The harvester was designed by Michigan State University researchers and built by Precise Manufacturing with funding from the USDA and the Michigan Apple Committee The in-field sorting harvester is just the first step in a fully robotic apple harvester/sorter “We built our first prototype in 2016 and our final improved version for use in 2020 ” says Renfu Lu agricultural engineer Michigan State University “The entire machine was designed to work with the sorting system Our next goal is to incorporate multiple robotic arms to pick the apples too ” The current self-propelled harvester has room for 6 workers 2 picking at ground level and 4 from adjustable height platforms on the harvester’s sides As they pick workers place apples on conveyor belts In the case of ground level workers conveyer arms controlled by the harvester operator follow them through the orchard Conveyer access is designed for minimal body and hand movements The apples are carried to a computer-vision sorting system Select apples are dropped into one bin while lower quality apples are deposited in a second bin Foam cushioned rollers catch and place individual apples preventing them from bumping into other apples Working at a speed of up to 12 apples per second the sorter is designed to match the picking speed of 6 workers Sorting in the field and eventual robotic picking could significantly reduce apple grower costs About half of grower production costs are tied up in picking and handling Mario VanDyke Precise Manufacturing worked with Lu to build the main chassis steering and hydraulic systems He notes that the harvester as it is now designed will not compete economically “A typical orchard would need to bring in multiple machines to get the apples harvested fast enough ” he says “Currently they can bring in 200 to 300 pickers at a time to get the job done ” He sees the real potential for the harvester coming with the addition of robotic picking arms Lu agrees “This is still an early stage ” says Lu “In the next 3 to 5 years we will have incorporated robotic picking ” Contact: FARM SHOW Followup Renfu Lu 524 S Shaw Lane 224 Farrall Hall East Lansing Mich 48824 ph 517 432-8062 or 517 749-3044; lur@msu edu or renfu lu@usda gov
To read the rest of this story, download this issue below or click
here to register with your account number.