2021 - Volume #45, Issue #2, Page #11
[ Sample Stories From This Issue | List of All Stories In This Issue | Print this story
| Read this issue]
He Buys, Repairs And Sells Auction Finds
![]() |
![]() |
“I retired from a career as an electrical engineer and started farming with a couple hundred acres,” explains Voss. “As I added more acres, I needed more equipment, and one thing led to another. I would go to the auction and see that one piece was pretty cheap compared to another that was in better shape.”
Voss figured he could spend a little time and money fixing up the lower cost equipment and still be money ahead. Along the way he learned to fix a lot of different types of equipment.
When he got into the hay business, he added fixing balers to his list. He quickly realized that while many people knew how to operate a baler, very few knew how to fix one. Before long he was buying balers, fixing them, and then reselling.
He still fixes up equipment for himself. When he needed a corn picker for limited corn acres, he hit the auction and found a 3-row pull-type.
“Usually, the snouts on old pickers are pretty well banged up,” notes Voss. “This one had some metal broken loose on one side of a snout and some worn through. It had been used a lot.”
Voss replaced the gathering chains and rebuilt the elevator chains and the husking bed, including all new rolls. “There were plastic brushes over the husking bed that were so brittle they broke right off,” says Voss. “The brushes and the gathering chains were the only parts I could get from Deere.”
Voss went online and was directed to JD Huskers, East Earl, Penn. They had everything he needed. (JD Huskers, ph 717 445-0990).
While Voss put a fair amount of time and money into the old picker, it looks and runs like new. “In its repaired condition, it is probably worth around $6,000,” he says. “It works fine for my needs and should for a good long time.”
Fixing equipment for his own use or resale usually means repainting it, which was one of his biggest challenges.
“Some people just squirt some paint on, but it’s a bit of an art to paint equipment well,” says Voss.
Hydraulics were another challenge at first, but now Voss works on them all the time. He pulls cylinders apart, replaces seals and replaces hoses with new ones he makes himself.
“I started out with a swaging tool,” says Voss. “It was set up for a particular size hose and fitting. Just put the hose in a hydraulic press and squeeze on the new fittings. Now I have a fancier machine that can do 90-degree fittings and more.”
Voss doesn’t understand why more farmers don’t make their own hoses. “I don’t know another farmer within 20 miles who makes his own hoses,” he says. “It’s not hard and saves money and time running to town.”
Voss is careful about the equipment he buys. Recently he picked up a 10-yard dirt scraper. The box had slipped out of line with the frame, but rather than fix it, the previous owner had welded steel plates on the side of the box to force it away from the frame. Other than that, it was in pretty good shape.
“We cut the plates off, took out all the bolts, and realigned it,” says Voss. “We rebuilt the hydraulic cylinders, installed new springs, and packed the wheel bearings and such. It didn’t even need new tires, which can be the biggest expense.”
The new springs, which cost $100 each, were his biggest out of pocket costs. “It was time consuming, but not expensive,” says Voss. “I paid $4,000 for it, and once I paint it, it will be worth $9,000 to $10,000.”
Contact: FARM SHOW Followup, Lar Voss, 27455 WCR 15, Johnstown, Colo. 80534 (ph 970 204-9300; lar@larvoss.com).
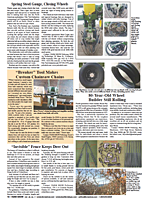
Click here to download page story appeared in.
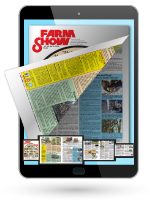
Click here to read entire issue
To read the rest of this story, download this issue below or click here to register with your account number.