You have reached your limit of 3 free stories. A story preview is shown instead.
To view more stories
(If your subscription is current,
click here to Login or Register.)
Walk-Behind Tractor Converted To Transplanter
When arthritis showed up in his knees, David Johnson started thinking about turning one of his David Brown walk-behind tractors into a transplanter.
“I set out 12 to 16 dozen tomato plants every spring, doing it like my dad,” says Johnson. “He would do it by sticking the trowel in, making space, dropping the pla
..........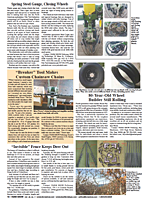
You must sign in, subscribe or renew to see the page.
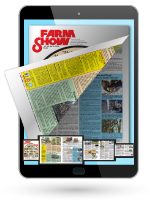
You must sign in, subscribe or renew to see the flip-book
Walk-Behind Tractor Converted To Transplanter CROPS New Techniques When arthritis showed up in his knees David Johnson started thinking about turning one of his David Brown walk-behind tractors into a transplanter “I set out 12 to 16 dozen tomato plants every spring doing it like my dad ” says Johnson “He would do it by sticking the trowel in making space dropping the plant in pulling the trowel out and stepping down the dirt When my arthritis showed up it became painful to do it that way ” Johnson had a lot to work with given his family’s love for walk-behind tractors “My dad bought his first in 1954 ” says Johnson “He always used 2 in the garden and started picking up used ones for parts ” It was a practice that Johnson continued Today he has 27 of the little workhorses Some are for parts and others for chores including 5 set up with various types of cultivators Setting up one as a transplanter just made sense The challenge was slowing down the ground speed “I knew I needed to make it super slow ” says Johnson “I bought a slow speed pulley but at 3/4 mile per hour it was still too fast ” Johnson’s solution was to install the hydraulic drive from a log splitter and an 8 hp Tecumseh engine into a tractor frame He mounted the pump reservoir and valve and plumbed them to run through a slow-speed hydraulic motor with the valve set at the detent position “The David Brown has a hand-operated clutch that allows it to free wheel when stopped ” says Johnson “With the motor belted to the clutch pulley I could start and stop as needed ” Aside from the used log splitter the only parts Johnson had to buy were an air filter for the Tecumseh and an opener for the transplanter “I ordered an irrigation shovel from Northwest Manufacturing to use as a planter shovel ” says Johnson “I built a framework out of salvaged 1 1/4 by 1/2-in steel and attached it to the chassis I mounted the 7-in shovel to a vertical shaft on the frame ” He attached a length of 3-in pvc pipe to the vertical shaft modifying it with a 3 to 3-in adapter at the top for a funnel when dropping in seedlings At the bottom of the pvc he cut away about 2/3 of the last 6 in of the pipe with the remaining third facing forward toward the shovel “The cut away lets the seedlings stay upright when dropped into the furrow ” explains Johnson To close the furrow over the seedling roots Johnson used an old Troy-Bilt hiller shaped like a V-plow He split it in two and mounted opposing pieces behind the pvc pipe to push dirt in instead of out A set of lawn mower wheels are mounted to the framework as press wheels At the very rear of the transplanter frame is a set of gauge wheels with hand levers for height adjustment from an old David Brown cultivator Johnson swapped out 14-in cutting discs for worn out 10-in wheels “The larger discs let me raise the frame to get the planter shovel off the ground when going between the garden and the garage ” he says To finish off the transplanter Johnson mounted a seedling tray stand to the right of the pvc tube “When I see the right distance between the pvc tube and the last seedling I stop the transplanter drop a seedling and move on ” says Johnson “It is a lot easier than doing it at ground level and I don’t think I have more than $450 in it ” Contact: FARM SHOW Followup David Johnson 8090 Benson Rd Carroll Ohio 43112 ph 740 504-5492; djos6@hotmail com
To read the rest of this story, download this issue below or click
here to register with your account number.