You have reached your limit of 3 free stories. A story preview is shown instead.
To view more stories
(If your subscription is current,
click here to Login or Register.)
Mower Conditioner Converted Into Low-Cost Compost Turner
A cousin’s offer of an 8-ft. Taarup rotary mower conditioner with a blown gearbox gave Ian Wyndlow a base machine he could turn into a compost turner.
“I got the idea from an article in FARM SHOW, ‘Low-Cost Compost Turner Great For Small Farmers’ (Vol. 44, No. 2),” says Wyndlow. “My dad and his twin brother had
..........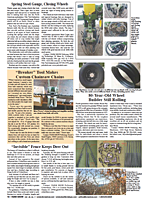
You must sign in, subscribe or renew to see the page.
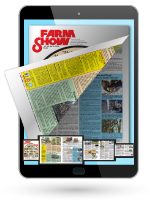
You must sign in, subscribe or renew to see the flip-book
Mower Conditioner Converted Into Low-Cost Compost Turner HAY & FORAGE HARVESTING Mowers 38 A cousin’s offer of an 8-ft Taarup rotary mower conditioner with a blown gearbox gave Ian Wyndlow a base machine he could turn into a compost turner “I got the idea from an article in FARM SHOW ‘Low-Cost Compost Turner Great For Small Farmers’ Vol 44 No 2 ” says Wyndlow “My dad and his twin brother had assembled a stockpile of parts from various machines and I was fortunate to inherit the inventory We had a salvaged Taarup gearbox from a 6-ft wide mower in inventory and I was delighted to finally justify having kept it ” Wyndlow removed the rotary cutter head completely and dropped the rear conditioner flair bar to where the cutter head had been He also replaced the damaged angle gearbox reduced the speed and increased torque with other modifications “I swapped out the high-speed sprockets for the lowest combination I could find in our inventory ” says Wyndlow “I thanked the spirit of my dad for the large wooden box of gears bearings sprockets and chain ” Wyndlow noticed that most compost turners had fairly large paddles arranged in a corkscrew pattern on the mixing shaft He knew this design was key to drawing material in from the edges and toward the center Eager to get the turner operational before fall rains he opted to use the forked tines already on the conditioner flair bar “I cut off and repositioned about 20 of the tines to produce a similar effect of bunching material toward the center ” says Wyndlow He then reshaped the existing steel cowling from the mower and some leftover 1/8-in steel fairings to fit the machine’s new purpose As he pulled the new turner into the compostables he discovered that even running his 80-hp tractor at an idle was too fast Riding the clutch slowed the speed down just enough “It does a terrific job of mixing and aerating the windrow ” says Wyndlow “I can straddle and mix a 4-ft high 8-ft wide and 200-ft long row in about 5 to 6 minutes ” Wyndlow says the turner did tend to flatten the windrow and spread it out to about 9 to 10 ft wide He modified the cowling at the rear to help direct material into a narrower windrow He also runs a front-end loader down the row to trim the sides back to about 7 ft wide “I think bigger paddles at a lower speed will be the ultimate answer ” says Wyndlow “However I figure it is achieving about 90 percent of the job I had hoped for and doing it quicker than blending materials with the front-end-loader ” Contact: FARM SHOW Followup Ian Wyndlow 13188 Doole Rd Ladysmith B C Canada V9G 1G6 ph 215 619-9760; ian@liquidstonestudios com
To read the rest of this story, download this issue below or click
here to register with your account number.