You have reached your limit of 3 free stories. A story preview is shown instead.
To view more stories
(If your subscription is current,
click here to Login or Register.)
540 Pto Converted To 1,000 Rpm
When Tony Negen upgraded tractors, he lost the use of his chipper. The older Kubota had a 1,000 rpm pto and the new one only had a 540. He solved that problem with a combination of jackshafts and pulleys. In the process, he realized he could drive a generator off the modified pto as well, so he extended the chipper pla
..........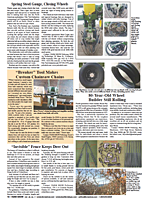
You must sign in, subscribe or renew to see the page.
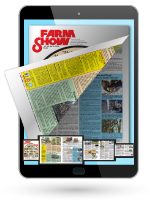
You must sign in, subscribe or renew to see the flip-book
540 Pto Converted To 1 000 Rpm POWER TAKE OFFS PTO S When Tony Negen upgraded tractors he lost the use of his chipper The older Kubota had a 1 000 rpm pto and the new one only had a 540 He solved that problem with a combination of jackshafts and pulleys In the process he realized he could drive a generator off the modified pto as well so he extended the chipper platform with a slide-on mount for the generator Since then he also modified a leaf vacuum so it can slide on in place of the generator when it is needed “I used a jackshaft and a combination of pulleys that let me gear up the pto speed for the chipper ” says Negen “The same drive belt is used for the chipper and the generator ” Getting the right pulleys in place was easy for Negen “I turned the problem over to my engineer son in Michigan and told him to figure it out ” says Negen “He put the formulas together and I followed them ” He wanted the best fuel economy when running the equipment The Kubota normally runs full throttle at 2 640 rpm The pulley combination lets him idle it down to around 1 800 while still achieving the right speed for both attachments Following his son’s formulas Negen mounted a 12-in driveshaft to the pto drive and ran a belt to a 4-in drive pulley on a 1-in jackshaft An 11 1/2-in pulley at the other end of the jackshaft drives a 7 1/2-in pulley on the chipper He put a 3-in pulley on the generator to be driven by the same belt as the chipper The frame the generator slides onto is made from square tubing to match the original frame of the chipper The mount is made with salvaged 1-in tubing and angle iron The angle iron base on the generator slides into the mount Negen hinged the generator to its base to make the drive belt self-tightening A spring-loaded pulley keeps tension on the drive belt from the pto shaft and on the belt to the chipper “I have a little slippage on that first belt ” says Negen “I went with a 1/2-in belt but I think a 5/8 would have been better when the generator is under load It can stretch when it is driving 6 000 volts with that 9 000-volt generator ” Negen designed the slip-out mount for the generator so he could remove it when using the dust producing wood chipper Adding the various attachments to the same base has been interesting but Negen admits he wouldn’t do it again “I would just put the generator on its own cart ” he says “I only get the chipper out every few years plus I have to take the bearing off the chipper to remove the belt I could avoid that completely ” Contact: FARM SHOW Followup Anthony Negen 88504 200th St Sacred Heart Minn 56285 ph 320 444-0723; 1944deerelover@gmail com
To read the rest of this story, download this issue below or click
here to register with your account number.