You have reached your limit of 3 free stories. A story preview is shown instead.
To view more stories
To view more stories
SUBSCRIBE OR RENEW NOW
(If your subscription is current, click here to Login or Register.)2021 - Volume #45, Issue #6, Page #36
[ Sample Stories From This Issue | List of All Stories In This Issue]
He “Strip-Crops” Livestock With Stock Cropper System
Zack Smith alternates strips of corn and soybeans with strips of forage where pens of livestock harvest the forage as it grows. It is a farming system that Smith calls Stock Cropping and he believes it could boost profits for small to mid-size farms. “I’m 41 and have done well with the existing, conventional, c..........
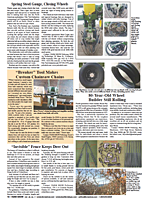
You must sign in, subscribe or renew to see the page.
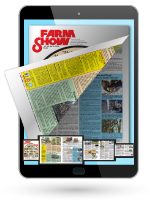
You must sign in, subscribe or renew to see the flip-book
He “Strip-Crops” Livestock With Stock Cropper System CROPS New Techniques Zack Smith alternates strips of corn and soybeans with strips of forage where pens of livestock harvest the forage as it grows It is a farming system that Smith calls Stock Cropping and he believes it could boost profits for small to mid-size farms “I’m 41 and have done well with the existing conventional commodity system the first half of my career ” says Smith “Now I’m trying to find the exact opposite a sustainable and affordable system that will make the farmer more money with the same amount of land ” Smith thinks his multi-species mobile Stock Cropper barns are the key They combine the benefits of his current strip-till and cover crop system with grazing Smith is now on his second working prototype The ClusterCluck MaX9 is 30-ft wide with 8 by 30-ft outside pens sandwiching two 8 by 15-ft pens inside the mobile “barn” The 8-ft deep pen on the front of the unit holds two calves that also access a floorless inside pen The 8-ft deep pen at the rear of the barn holds 10 Berkshire feeder pigs They access the other half of the interior which is outfitted with Tenderfoot a plastic-coated slat flooring The barn has an inverted V galvanized roof that captures rainwater and directs it to two storage tanks Feeding stations on the inside augment the forage the calves and pigs access in their grazing pens The MaX9 is designed to be pulled down 30-ft wide strips of mixed forage between 30-ft strips of cash crops Electric jacks lift the barn and the pens off the ground 12 in The unit is pulled forward 8 ft twice a day to provide fresh forage Two large steel wheels at each end of the barn carry the unit forward and swivel as the unit is pulled around to the next forage strip Two large panels on each side of the MaX9 can be propped open providing shade over the exterior pens while providing airflow to the interior “The goal is to get the 400-lb steers to 900 to 1 000 lbs and the Berkshire hogs to market weight by the end of the cropping season ” says Smith “Daily maintenance takes about 20 min which includes adding feed and water with time to observe the animals ” Smith’s first prototype was 18-ft wide with 11-ft deep pens front and rear It housed four goat kids and four lambs in the forward pen with 10 feeder pigs in the rear pen Each pen had access to a 9 by 11-ft interior Two 9 by 11-ft chicken pens holding 185 broilers between them followed behind Smith says that after a full season using the first prototype he’s convinced the new method has great potential “It was an incredible success and we didn’t lose a single animal ” says Smith who then broke out the financials The cost of the structure was $15 000 which amortized over seven years came to $2 600 per year The animals cost $1 870 with another $1 871 for supplemental feed Total annual expenses for the barn animals feed expected repairs pasture rent labor 20 min per day at $30 per hour and machinery came to $8 225 20 Total livestock revenue came to $10 401 before processing “This gave us a profit per barn on an acre of land at about $2 200 ” says Smith “We hoped it would be higher but that didn’t include benefits to the neighboring strips of corn ” Smith increased seed population and nitrogen applications to the outside rows of corn to take advantage of increased sunlight He harvested 262 bushels of corn per acre at $4 per bushel for a net profit of $398 He compared that to his conventional fields of solid corn which yielded 210 bushels with less seed and N cost for a net profit of $165 per acre “When I add the corn enterprise and the livestock profits averaged over two acres I had a total profit of $1 286 per acre or seven times the conventional corn acre ” says Smith “Stacking enterprises like we did realized a significantly higher net profit ” Smith also identified challenges to his system Limited meat processing windows forced him to market the hogs 10 days earlier than planned The resulting 20 lbs lighter weight made a big difference to the bottom line “I also think we could have increased the stocking rate of the chickens which combined with increased finishing weights on the hogs could have doubled our profitability ” says Smith Smith’s goal is to prove out the concept both its financial and agronomic benefits Initially he hopes to encourage smaller row crop farmers to adopt a Stock Cropper system to raise meat animals for their own use and local sales The MaX9 which was professionally fabricated is the first step in the process Ideally an established manufacturer would take over production “If we can get it off the ground we can start working toward economies of scale in fabricating as well as processing perhaps having our own Stock Cropper meat brand and centralized processing ” says Smith “The ideal would be to have 30 barns traveling down 30 acres of an 80-acre field with the remainder in crops and laneways for turning the barn ” Smith invites readers to follow him on Twitter and Facebook as well as on his YouTube channel for updates on Stock Cropper development Contact: FARM SHOW Followup The Stock Cropper 45982 180th Ave Lake Mills Iowa 50450 ph 641-512-0379; thestockcropper@gmail com; www thestockcropper com
To read the rest of this story, download this issue below or click here to register with your account number.