2021 - Volume #45, Issue #6, Page #40
[ Sample Stories From This Issue | List of All Stories In This Issue | Print this story
| Read this issue]
Built-From-Scratch “Deere Cat” Tractor
![]() |
![]() |
![]() |
![]() |
![]() |
“I’ve had so many people just amazed at seeing it and trying to figure out what went into it,” says Fenske, a retired commercial welder and machinist.
Aside from the 70 Deere and the restored 1940’s Cat engine, he used parts off an old 3/4-ton Chevy 4-WD front end. All machine work and fabrication were done by Fenske at his farm shop. He started the project in 2019, working on it as he had time. “Occasionally, I had to just walk away from it,” he recalls.
He started by tearing down the Deere 70 his father bought in the 1970’s. It sat in Fenske’s boneyard after the engine quit. He set aside the front axle and steering column but removed everything else ahead of the crankshaft housing.
Fenske purchased the Cat engine as part of a genset that once powered a refrigerated railcar. Initially, he thought to turn the generator into a welder, but it didn’t have the flexibility he wanted.
“It hadn’t run for 25 years,” says Fenske. “I hooked up a couple of batteries, added some starting fluid, and it started right up.”
With its 3 1/2-in. bore and 5-in. stroke, he knew it had lots of torque. It also required lots of room. Fenske created a new frame using heavy-angle iron. Heavy 5 by 7-in. rectangular tubing welded to the angle iron extended forward to support the engine.
“I put new Timken bearings on the front spindles to handle the weight of the engine,” says Fenske. “I also shortened the spindles by 5 in. to adjust for the new frame.”
The first challenge he faced was to build a transfer case or right-angle gearbox between the in-line Cat engine and the crossways Deere drive. It needed to mount to the tractor and the larger bell housing of the engine.
“I had no prototype or mockup,” says Fenske. “I just started where the Deere block was bolted to the crankshaft housing and went forward.”
Fenske used a section of 1-in. thick, square steel tubing he had on hand to make a gearbox housing. He mounted it at a 45-degree angle because the Chevy differential was too wide to fit in the square tubing if it was mounted at a 90-degree angle.
To match the bell housing, Fenske used a 1-in. steel plate machined to make the transition from round bell housing to square gear housing. A flange salvaged from the generator and matching the engine bell housing was welded to the plate.
“I could've used a 3/4-in. plate, but I had the 1-in. plate sitting around, so I used it,” says Fenske.
What was also available was a silent chain sprocket and chain. Silent chains are built more heavy-duty than regular roller chain. The downside is that Fenske needed a second and smaller sprocket. He had to machine that from scratch.
“I cut it from 2 1/2-in. steel plate,” says Fenske. “I didn’t have a silent chain milling cutter, so I made one by reprofiling a cutter for making gears. I had to recut the sprocket several times to get the correct pitch diameter. I started out using specs from a gear, but silent chain sprockets are a little different.”
His biggest challenge came as he machined a tapered spline on the clutch end of the new shaft that replaced the Deere crankshaft. He recognized that the driving disk had to end up in just the right position, not too deep, yet not sticking out too far.
He cut down the front axle and differential so they would fit in the square tube housing. That required him to recut the axle splines.
“The axle shafts were heat-treated, so when I recut the splines, I had to turn the cutter slowly and use lots of fluid,” says Fenske.
He built the chain case right on the tractor. He started with plates bolted to the right-angle gearbox and the tractor’s main bearing and built out from there, assembling parts as he went.
“Once I had it tacked together, I pulled the assembly off and welded it together,” says Fenske. “When all the welding was complete, it had distorted the chain case some, and I had to adjust a few mounting holes with a die grinder.”
He replaced the old fuel tank with a new tank fabricated to sit under the tractor seat. He also added a battery box to the rear end with room for two 12-volt batteries for the 24-volt electrical system on the engine. He positioned it so he could top it with a step for mounting from the rear.
The original Deere steering post was mounted on the side rather than in front. A universal joint added to the steering shaft made the change work. Like the original Deere 70, the Deere Cat has manual steering.
“When it's sitting still, I can’t turn the front wheels, but if it is moving, it’s not a problem,” says Fenske. “Even with the additional weight on the front end, it’s no worse steering than the 70 was originally.”
The Deere Cat uses the original Deere oil pump system to lubricate the main bearings and the chain case. He added a separate oil pressure gauge to monitor it.
Fenske pushed hard to get the Deere Cat done in time for a local show this summer. He managed to get it running a few days before the show, and it worked great. He's even raked hay with it. At the Lake Itasca Region Pioneer Farmers show, he belted it up to power the club’s flat belt machine shop.
One thing he's not planning to do is to add sheet metal to cover up the work he did. “I plan to keep it open,” he says. “When I was working on it, my wife said, ‘You’ll never be able to sell it because no one will be able to get parts. I told her I had no plans to sell it in my lifetime. I have too much of me in it.”
Contact: FARM SHOW Followup, Gerald Fenske, 3707 Madison Ave. SW, Bemidji, Minn. 56601 (ph 218-444-6862; creatensteel@gmail.com; www.machinesandmetalworkinginnorthernminnesota.com).
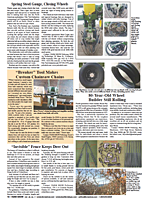
Click here to download page story appeared in.
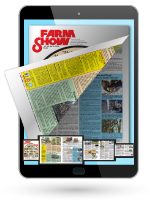
Click here to read entire issue