You have reached your limit of 3 free stories. A story preview is shown instead.
To view more stories
(If your subscription is current,
click here to Login or Register.)
Big Forage Baler Makes Compact Bales For Export
The first Kadant Paal HTR 625 baler made especially for the export of products such as corn, alfalfa, ryegrass and straw has been used in Europe since 1992. These 2-ram stationary machines were designed to handle wet, unique or difficult products plus much of the European alfalfa crops destined for export to China and
..........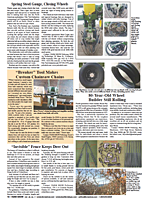
You must sign in, subscribe or renew to see the page.
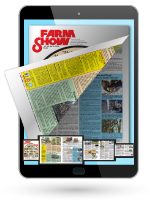
You must sign in, subscribe or renew to see the flip-book
Big Forage Baler Makes Compact Bales For Export BALERS The first Kadant Paal HTR 625 baler made especially for the export of products such as corn alfalfa ryegrass and straw has been used in Europe since 1992 These 2-ram stationary machines were designed to handle wet unique or difficult products plus much of the European alfalfa crops destined for export to China and the Middle East Kadant Paal’s factory in the northwest of Germany has manufactured more than 40 units scattered around the world with most placed in Europe and a single machine in the U S Balers are normally situated in export facilities and represent the last stop before forage or straw is loaded into shipping containers and exported abroad Agricultural forages are brought to the baler by large farmers or commercial exporters Models offered are electrically run and sport either a 2 by 73 hp or 3 by 73 hp power pack system “The hay or straw comes in big trucks or in round bales but we always have to open everything and check the humidity ” says Oriol Juvanet Export Area Manager for South America and the Middle East “If the moisture is good we can bale If not we must wait for it to dry in the field or mechanically dry it at the factory It never goes directly from the field to the baler because the humidity is too high ” Once the forage material is determined to be between 11 and 12 percent humidity it’s fed into the high-capacity high-density baler Juvanet outlines three reasons why the HTR 625 is superior to competitive models First the compacting and tying is a continuous system “The tying is outside the chamber so we can compact a bale at the same time the previous one is tying This is the opposite of our competitors and we do it with the same power Plus our throughput is higher than other companies ” Juvanet explains Next the baler uses plastic straps to tie which are lower cost and safer for the animals eating the feed Lastly the design technology and conception are high flow high performance at a low energy cost For example a blade system reduces cutting forces against the material and the hydraulic block for compaction is mounted directly on the cylinder avoiding heat-producing pipes that reduce pump productivity Kadant Paal is interested in expanding further into the U S claiming they offer the cheapest solutions with the best results They believe the proof of this is that many of their customers buy more than one unit The standard 3 by 73 hp model price is approximately $950 000 Contact: FARM SHOW Followup Glenn Marsh Kadant Paal LLC 1425 Kingsview Drive Lebanon Ohio 45036 ph 513-229-8181; paal-usa service@kadant com; www kadantpaal com
To read the rest of this story, download this issue below or click
here to register with your account number.