Biomass Burner Dries Grain Faster, Cheaper
 ✖  |
BioDryAir from Triple Green Products burns biomass to reduce grain-drying costs by up to 80 percent over natural gas or propane. Hot, dry clean air is piped into a conventional drier; no heat exchanger is needed. Even better for Canadian readers of FARM SHOW, a government program currently covers half the cost of BioDryAir systems.
“The Agricultural Clean Technology Act (ACT) can be used for a new energy-efficient grain dryer or for retrofitting an existing dryer with an energy-efficient system like BioDryAir,” says Lyall Wiebe, Triple Green.
While a similar program is not available in the U.S., the carbon-neutral BioDryAir systems may impact farm income as carbon markets develop. However, the ROI with the systems should be enough for most farmers to consider the burners.
“The typical ROI on a system is between two and five years, but we’ve had systems pay for themselves in one year,” says Wiebe. “As gas prices climb, the ROI improves.”
Unlike propane combustion that creates water vapor as the propane burns, biomass combustion in the BioDryAir system produces only dry heat. This enhanced efficiency creates a rapid ROI when switching from propane.
BioDryAir systems can produce from 5 to 30 million Btu depending on the unit’s size. For even larger heat output, they can be stacked as needed, explains Wiebe.
One of the attractive features of the BioDryAir systems is that they can be installed as a parallel heat source on an existing dryer. The operator simply switches the hot air input from the gas-fired burner to the biomass system or back as needed.
“If a customer runs out of biomass fuel near the end of the drying season, they can easily switch back to a gas-fired burner,” says Wiebe.
The BioDryAir system was adapted to grain dryers from technology in use for more than 20 years in the aggregate industry and municipal heating systems. Wiebe says installation prices vary by size, location and various other factors.
“We use under-the-fire and over-the-fire air flows to burn the biomass plus all the released gasses,” explains Wiebe. “The dual burns at 1,800 degrees and leaves no smoke or particulates in the hot air.”
The complete burn is effective with all types of biomass, from wood chips and pellets to corn stover, oat hulls and even highly acidic materials. “We have systems burning very acidic miscanthus grass and chicken litter, and they’ve been doing it for years,” says Wiebe.
The stoker system/burn chamber is designed for longevity and efficiency. The burn chamber is 1/4-in. steel lined with 6 in. of insulation, which is in turn lined with 6 in. of refractory material designed to withstand the high temperatures. The stoker is a rotating chain bed composed of 1/5-in. thick, 2-in. wide and 6-in. long steel links. It provides 1/8-in. gaps for the under-the-fire air to be forced up and through the burning biomass. Material is pushed onto the chain bed by a multi-screw system.
“We have district heating systems that have run for 20 years and shut down for maintenance for only one day a year,” says Wiebe. “A farmer using the same basic system for a few weeks a year should be able to pass it down to his children and grandchildren.”
In fact, the heating system should outlast multiple drying systems. Installed on an existing dryer, it can replace an outdated gas-fueled heating system.
“Grain dryers have to meet certain standards to operate, and at some point, they no longer pass inspection,” says Wiebe. “Our system can be used with a dryer that no longer meets gas-fired inspection criteria.”
Contact: FARM SHOW Followup, Triple Green Products, Box 119, R.R.1, Morris, Manitoba Canada R0G 1K0 (ph 204-746-6333; toll free 855-373-2378; info@triplegreenproducts.com; www.triplegreenproducts.com).
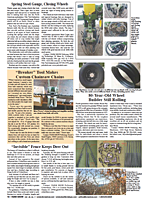
Click here to download page story appeared in.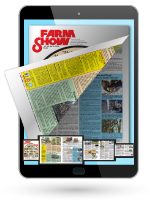
Click here to read entire issue
Biomass Burner Dries Grain Faster Cheaper ENERGY Alternative Fuels BioDryAir from Triple Green Products burns biomass to reduce grain-drying costs by up to 80 percent over natural gas or propane Hot dry clean air is piped into a conventional drier; no heat exchanger is needed Even better for Canadian readers of FARM SHOW a government program currently covers half the cost of BioDryAir systems “The Agricultural Clean Technology Act ACT can be used for a new energy-efficient grain dryer or for retrofitting an existing dryer with an energy-efficient system like BioDryAir ” says Lyall Wiebe Triple Green While a similar program is not available in the U S the carbon-neutral BioDryAir systems may impact farm income as carbon markets develop However the ROI with the systems should be enough for most farmers to consider the burners “The typical ROI on a system is between two and five years but we’ve had systems pay for themselves in one year ” says Wiebe “As gas prices climb the ROI improves ” Unlike propane combustion that creates water vapor as the propane burns biomass combustion in the BioDryAir system produces only dry heat This enhanced efficiency creates a rapid ROI when switching from propane BioDryAir systems can produce from 5 to 30 million Btu depending on the unit’s size For even larger heat output they can be stacked as needed explains Wiebe One of the attractive features of the BioDryAir systems is that they can be installed as a parallel heat source on an existing dryer The operator simply switches the hot air input from the gas-fired burner to the biomass system or back as needed “If a customer runs out of biomass fuel near the end of the drying season they can easily switch back to a gas-fired burner ” says Wiebe The BioDryAir system was adapted to grain dryers from technology in use for more than 20 years in the aggregate industry and municipal heating systems Wiebe says installation prices vary by size location and various other factors “We use under-the-fire and over-the-fire air flows to burn the biomass plus all the released gasses ” explains Wiebe “The dual burns at 1 800 degrees and leaves no smoke or particulates in the hot air ” The complete burn is effective with all types of biomass from wood chips and pellets to corn stover oat hulls and even highly acidic materials “We have systems burning very acidic miscanthus grass and chicken litter and they’ve been doing it for years ” says Wiebe The stoker system/burn chamber is designed for longevity and efficiency The burn chamber is 1/4-in steel lined with 6 in of insulation which is in turn lined with 6 in of refractory material designed to withstand the high temperatures The stoker is a rotating chain bed composed of 1/5-in thick 2-in wide and 6-in long steel links It provides 1/8-in gaps for the under-the-fire air to be forced up and through the burning biomass Material is pushed onto the chain bed by a multi-screw system “We have district heating systems that have run for 20 years and shut down for maintenance for only one day a year ” says Wiebe “A farmer using the same basic system for a few weeks a year should be able to pass it down to his children and grandchildren ” In fact the heating system should outlast multiple drying systems Installed on an existing dryer it can replace an outdated gas-fueled heating system “Grain dryers have to meet certain standards to operate and at some point they no longer pass inspection ” says Wiebe “Our system can be used with a dryer that no longer meets gas-fired inspection criteria ” Contact: FARM SHOW Followup Triple Green Products Box 119 R R 1 Morris Manitoba Canada R0G 1K0 ph 204-746-6333; toll free 855-373-2378; info@triplegreenproducts com; www triplegreenproducts com
To read the rest of this story, download this issue below or click
here to register with your account number.